Loctite 620 vs 680: Which Adhesive is Best for Your Project?
Choosing the right adhesive can make or break your project, especially when it comes to high-performance applications. If you’re comparing Loctite 620 and 680, you’re likely dealing with critical bonding needs. Both of these anaerobic adhesives excel in securing cylindrical parts, but each has unique properties that suit different scenarios.
Loctite 620 is known for its high-temperature resistance, making it ideal for applications where heat is a major factor. On the other hand, Loctite 680 offers superior gap-filling capabilities and high strength, perfect for situations requiring robust bonding. Understanding the differences between these two can help you make an well-informed choice and ensure the success of your project.
Key Takeaways
- High-Temperature Applications: Loctite 620 is ideal for applications up to 450°F (232°C), making it perfect for high-heat environments such as automotive exhaust systems and industrial gearboxes.
- Chemical Resistance: Loctite 620 provides strong chemical resistance, ensuring durability against harsh substances, whereas Loctite 680 offers moderate resistance sufficient for common industrial chemicals.
- Gap-Filling Capabilities: Loctite 680 excels in filling larger gaps up to 0.25 mm with its low viscosity, making it suitable for precise assemblies like bearings, bushings, and sleeves.
- Viscosity and Flow: Loctite 680’s low viscosity allows it to flow easily into tight fittings, ensuring robust bonds in precision engineering tasks, while Loctite 620 has high viscosity suited for applications requiring gap bridging.
- Application Suitability: Choose Loctite 620 for high-temperature, high-stress environments and Loctite 680 for applications needing precise fitment and low-viscosity bonding.
- Industry Use Cases: Both adhesives serve critical roles in various industries, from automotive and heavy machinery to specialized industrial equipment, with each product tailored to meet specific operational demands.
Key Features of Loctite 620
Loctite 620 is renowned for its resilience in high-temperature environments and robust bonding properties. Here’s a closer look at its key features:
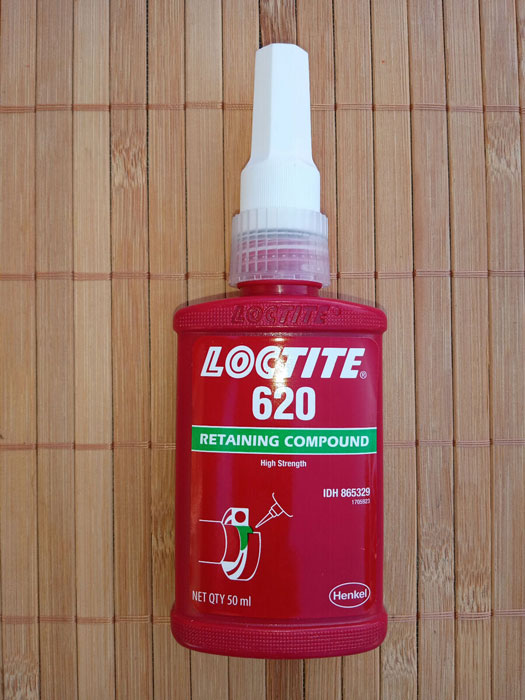
Temperature Resistance
- High-Temperature Tolerance
- Loctite 620 withstands temperatures up to 450°F (232°C), making it ideal for applications where heat resistance is crucial.
- Suitable for high-heat applications including bonding parts in automotive and industrial settings.
Chemical Resistance
- Strong Chemical Resistance
- Provides exceptional resistance against various chemicals, ensuring a durable bond even in challenging environments.
- Effective in preventing bond degradation due to exposure to harsh substances.
Application Areas
-
Cylindrical Fittings
- Designed specifically for bonding cylindrical fitting parts, particularly suitable for slip-fit assemblies.
- Useful in preventing metal fretting, corrosion, and sealing against leakage.
-
Gap-Filling Abilities
- Accommodates gaps up to 0.015 inches (0.38 mm) diametral clearance, allowing it to fill larger spaces between bonded parts.
- Often utilized in high-strength and high-temperature applications, such as automotive engines and industrial machinery.
This adhesive ensures reliability and efficiency in maintaining the integrity of bonded components under high operational stress.
For comparison, here’s a detailed table outlining the key differences between Loctite 620 and Loctite 680:
Feature | Loctite 620 | Loctite 680 |
---|---|---|
Max Temperature | 450°F (232°C) | 300°F (149°C) |
Chemical Resistance | Strong | Moderate |
Gap Filling | 0.015 inches (0.38 mm) | Greater gap-filling |
High Temperature | Suitable | Lower tolerance |
Use Loctite 620 when you need a reliable solution in high-temperature applications where strong chemical resistance and gap-filling are crucial.
Key Features of Loctite 680
Loctite 680 is another high-performance adhesive designed for bonding cylindrical parts. Here are its key features:
Temperature Resistance
Loctite 680 offers good temperature resistance, tolerating conditions up to 300°F (149°C). This makes it suitable for applications where moderate heat exposure is expected without compromising its integrity.
Chemical Resistance
While the chemical resistance of Loctite 680 isn’t as robust as that of Loctite 620, it still provides effective protection against common industrial chemicals. This includes various oils, fuels, and water, making it reliable in less chemically aggressive environments.
- Cylindrical Fitting: Loctite 680 excels when used for bonding cylindrical fitting parts. This includes applications such as securing bearings onto shafts and fixing bushings or sleeves.
- Low Viscosity: Its low viscosity enables it to flow easily into tight fitting assemblies, ensuring complete coverage and robust bonding. This feature is particularly advantageous for precision engineering tasks.
Comparing Loctite 620 and 680:
Feature | Loctite 620 | Loctite 680 |
---|---|---|
Temperature Resistance | Up to 450°F (232°C) | Up to 300°F (149°C) |
Chemical Resistance | Strong against various chemicals | Good with common industrial chemicals |
Application | High-temperature cylindrical assemblies | Low-viscosity cylindrical fitting |
Use Loctite 680 for bonding when moderate temperature resistance and good chemical protection are required, especially for precise cylindrical part fitting.
Comparative Analysis: Loctite 620 vs 680
When selecting between Loctite 620 and 680, understanding their key differences ensures success in your application. Both adhesives are strong and suitable for bonding cylindrical parts but excel in distinct environments and requirements.
Strength and Durability
- Loctite 620: This high-strength retaining compound is ideal for cylindrical fittings. With a temperature tolerance of up to 450°F (232°C), it’s suitable for high-heat environments. But, it may not perform as well with passivated metals, often found in AR15 receivers.
- Loctite 680: Also a high-strength compound, Loctite 680 is known for its low viscosity, allowing it to fill gaps up to 0.25 mm. It provides excellent curing performance on all metals, making it reliable for precise fitment applications.
Application Suitability
- Loctite 620: Often recommended for barrel bedding in firearms, specifically for mating the barrel extension to the upper receiver. The compound’s effectiveness can be constrained by the metal surfaces’ passivation.
- Loctite 680: Preferred for applications requiring precise fitment, such as securing bearings onto shafts or fixing bushings and sleeves. The low viscosity ensures complete coverage in tight-fitting assemblies, providing robust and reliable bonds.
Cost Effectiveness
When comparing cost, considering the specific application’s needs helps determine overall effectiveness. While both products have similar pricing, the detailed requirements of your project might make one more cost-effective than the other.
Feature/Specification | Loctite 620 | Loctite 680 |
---|---|---|
Strength | High | High |
Temperature Tolerance | Up to 450°F (232°C) | Up to 300°F (149°C) |
Viscosity | High | Low |
Gap Filling Capacity | Up to 0.015 inches (0.38 mm) | Up to 0.25 mm |
Suitable Applications | Barrel bedding, high-heat areas | Bearings, bushings, sleeves |
Chemical Resistance | Strong | Moderate |
Selecting between Loctite 620 and 680 involves balancing temperature tolerance, application specifics, and cost parameters. This careful evaluation ensures optimal performance, enhancing the durability and reliability of your projects.
Use Cases and Industry Applications
Loctite 620 and 680 serve unique roles across various industries, providing high-strength solutions for bonding cylindrical fittings. These products excel in different environments, tailored to meet specific operational demands.
Automotive Industry
- Loctite 620: In the automotive sector, Loctite 620 is often used for bonding components subjected to high temperatures such as:
- Exhaust Systems: High-temperature resistance ensures no loosening.
- Powertrain Components: Excellent durability against heat and vibration.
- Gearboxes: Prevents leakage and loosening in high-heat conditions.
- Loctite 680: Preferred for precise and low-viscosity applications, it’s ideal for:
- Bearing Assembly: Low viscosity allows complete penetration.
- Transmission Systems: Ensures a tight fit and strong bond.
- Bushing Fixations: Maintains structural integrity without gaps.
Heavy Machinery
- Loctite 620: Utilized for machinery operating under extreme conditions, including:
- Hydraulic Pumps: High viscosity ensures a solid bond even with minor gaps.
- Industrial Gearboxes: High-temperature tolerance provides stability in demanding environments.
- Mining Equipment: Withstands heavy shock and vibration.
- Loctite 680: Suitable for applications where precise fitting is crucial, such as:
- Rotary Shafts: Ensures no movement within the housing.
- Roller Bearings: Low viscosity fills tight spaces efficiently.
- Electric Motors: Secures components to prevent misalignment.
Technical Comparison
Feature | Loctite 620 | Loctite 680 |
---|---|---|
Gap Fill | 0.15 mm to 0.25 mm (0.006″ – 0.01″) | Up to 0.25 mm |
Operating Temperature | -55°C to 230°C (-65°F to 450°F) | Up to 149°C (300°F) |
Viscosity | High viscosity (8000 mPa·s) | Low viscosity |
Applications | Shafts, gears, pulleys in high-temperature environments | Bearings, bushings, sleeves in precise assemblies |
- Both Loctite 620 and 680 offer high-strength bonding solutions.
- Loctite 620 excels in high-temperature and vibration-intensive environments.
- Loctite 680 suits precise assemblies requiring low viscosity.
- Select based on application specifics including gap fill and temperature resistance.
Conclusion
Choosing between Loctite 620 and 680 depends on your specific application needs. If you’re dealing with high-temperature environments and require strong chemical resistance, Loctite 620 is your go-to adhesive. Its ability to handle temperatures up to 450°F (232°C) and fill gaps up to 0.015 inches makes it ideal for demanding conditions.
On the other hand, if you need superior gap-filling capabilities and strength for precise cylindrical part fitting, Loctite 680 is the better choice. It offers good temperature resistance up to 300°F (149°C) and effective protection against common industrial chemicals, making it perfect for securing bearings and fixing bushings.
Understanding your project’s requirements in terms of temperature tolerance, chemical resistance, and gap-filling needs will guide you in making the right decision. Both adhesives offer high-strength bonding solutions tailored to specific applications, ensuring optimal performance and reliability.
Frequently Asked Questions
What is the main difference between Loctite 620 and Loctite 680?
Loctite 620 is designed for high-temperature applications and offers excellent chemical resistance, making it suitable for environments up to 450°F (232°C). Loctite 680, on the other hand, excels in gap-filling and is ideal for precise cylindrical part fitting with moderate temperature resistance up to 300°F (149°C).
What applications is Loctite 620 best suited for?
Loctite 620 is best suited for high-temperature applications such as automotive exhaust systems, powertrain parts, hydraulic pumps, and industrial gearboxes. It is also commonly used for barrel bedding in firearms.
What is Loctite 680 primarily used for?
Loctite 680 is primarily used for securing bearings onto shafts, fixing bushings or sleeves, and other precise cylindrical part assemblies that require moderate temperature resistance and effective protection against common industrial chemicals.
How does Loctite 620 cure?
Loctite 620 cures anaerobically, meaning it hardens in the absence of air when confined between close-fitting metal surfaces. The typical cure time is up to 72 hours, depending on the substrate, bondline gap, and temperature.
Can both Loctite 620 and 680 withstand chemical exposure?
Yes, both Loctite 620 and 680 offer protection against industrial chemicals, though Loctite 620 provides a higher degree of chemical resistance, making it more suitable for challenging environments.
What temperature can Loctite 680 withstand?
Loctite 680 can withstand temperatures up to 300°F (149°C), making it suitable for moderate temperature applications such as transmission systems and electric motors.
Is Loctite 620 suitable for large gap filling?
Yes, Loctite 620 is suitable for accommodating larger gaps, with the ability to fill diametral clearances up to 0.015 inches (0.38 mm). This makes it effective for bonding components with slight imperfections or wear.
How does the cost-effectiveness of Loctite 620 and 680 compare?
Both Loctite 620 and 680 are similarly priced. However, the specific requirements of a project may make one more cost-effective than the other, depending on factors like temperature tolerance, application specifics, and chemical resistance needs.