Is JB Weld Oil Resistant? A Complete Guide for Your Auto Repairs
When it comes to repairing metal surfaces or sealing cracks, JB Weld often tops the list of go-to solutions. But if you’re dealing with oil exposure, you might wonder, “Is JB Weld oil resistant?” Understanding the durability and resistance of JB Weld in oily environments can save you time, money, and frustration.
Whether you’re fixing a cracked oil pan or sealing a leaky engine component, knowing if JB Weld can withstand oil is crucial. In this text, we’ll jump into the specifics of JB Weld’s oil resistance, helping you make an well-informed choice for your next repair project.
Key Takeaways
- Oil Resistance: JB Weld is generally considered oil-resistant once fully cured, making it reliable for repairs involving oil exposure, such as oil pans and engine components.
- Temperature Tolerance: Standard JB Weld withstands temperatures up to 500°F (260°C), while JB Weld Stick and Quick Weld variants endure up to 300°F (149°C), offering versatility for different repair needs.
- Application Process: Proper surface preparation, accurate mixing, and precise application are crucial to achieving effective and durable repairs with JB Weld.
- Curing Time: Allow JB Weld to fully cure—taking 15-24 hours at room temperature—to ensure maximum strength and oil resistance.
- User Experiences: Various real-life scenarios affirm JB Weld’s effectiveness in oil-exposed environments, provided that manufacturer guidelines are closely followed.
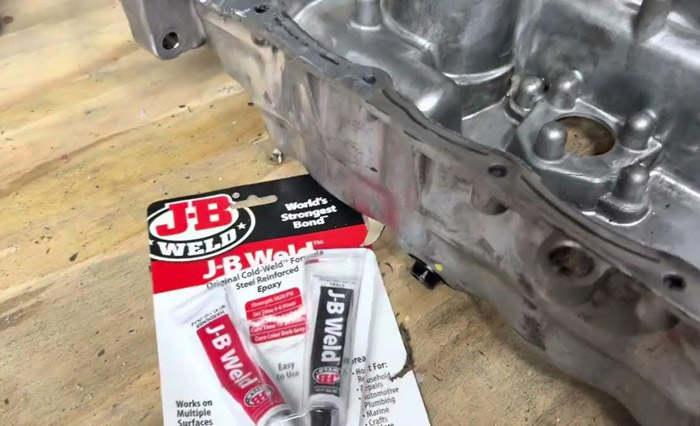
Strength and Durability
JB Weld, a widely-used adhesive, offers remarkable durability when appropriately applied and cured. Proper surface preparation and adherence to the manufacturer’s instructions are crucial to ensuring its effectiveness. Users often report successful repairs in various automotive applications like oil pans and oil lines, indicating that JB Weld can endure significant mechanical stress.
Temperature Resistance
JB Weld exhibits high-temperature resistance, making it suitable for a range of applications. The standard JB Weld product withstands temperatures up to 500°F (260°C). But, the stick and quick weld variants have a lower resistance of up to 300°F (149°C). This versatility allows you to select the variant that best suits your specific needs, whether dealing with high-heat environments or standard repairs.
Oil Resistance
JB Weld is generally considered oil-resistant once fully cured. It’s resistant to water and most petroleum products, including gasoline and oil. This characteristic makes it ideal for situations involving oil exposure, such as repairing oil pans and sealing oil lines. Users often choose JB Weld for tasks requiring a durable, oil-resistant adhesive.
Product Variant | Temperature Resistance | Application Examples |
---|---|---|
JB Weld Standard | Up to 500°F (260°C) | Oil pans, engine components |
JB Weld Stick | Up to 300°F (149°C) | Quick repairs, minor fixes |
JB Weld Quick Weld | Up to 300°F (149°C) | Rapid bonding needs |
Application Process
To ensure JB Weld’s oil resistance, follow precise steps for optimal bonding and durability. Meticulous preparation and application are key to achieving effective repairs.
Surface Preparation
Proper surface preparation ensures a strong bond. Follow these steps:
- Cleaning: Remove oil, dirt, and contaminants from the surface. Use a degreaser or acetone for thorough cleaning.
- Roughening: Sand the surface with medium-grit sandpaper. This creates a texture for better adhesion.
- Drying: Ensure the surface is completely dry before applying the epoxy.
Mixing Instructions
For the best results, mix JB Weld components correctly. Follow these steps:
- Ration: Combine equal parts of the resin and hardener from the package.
- Mixing: Stir the components thoroughly until you achieve a uniform color and consistency.
- Timing: Use the mixture within 4-6 minutes to avoid premature curing.
Application Techniques
Applying JB Weld accurately enhances its effectiveness. Adhere to these techniques:
- Coverage: Apply the mixed epoxy to the prepared surface, covering the entire repair area.
- Thickness: Ensure the application is thick enough to fill cracks but smooth enough for a neat finish.
- Tooling: Use a spatula or brush to evenly spread the epoxy. Remove excess material to avoid uneven surfaces.
Curing Time
Curing time determines the epoxy’s strength and oil resistance. Consider these factors:
- Initial Cure: JB Weld sets within 4-6 hours at room temperature (70°F).
- Full Cure: Achieves full strength after 15-24 hours. For optimal oil resistance, allow a full curing period.
- Temperature Sensitivity: Higher temperatures accelerate curing, while lower temperatures slow it down.
Aspect | Time | Condition |
---|---|---|
Initial Cure | 4-6 hours | Room Temp |
Full Cure | 15-24 hours | Room Temp |
Temperature | Accelerated | > 70°F |
Temperature | Delayed | < 70°F |
Using JB Weld for oil-resistant repairs involves careful surface preparation, accurate mixing, proper application techniques, and allowing sufficient curing time.
Terms:
Degreaser: A cleaning agent used to remove oil and grease from surfaces.
Resin and Hardener: Two components of JB Weld that chemically react to form a strong bond.
Smooth transitions between these steps ensure coherence throughout the process. Properly following these guidelines guarantees the durability and effectiveness of your JB Weld repairs.
Testing Oil Resistance
It’s crucial to know how well JB Weld performs under oil exposure, especially if you’re using it to fix parts like oil pans or engine components. Understanding its chemical and temperature resistance helps you make informed repair decisions.
Laboratory Tests
Manufacturers design JB Weld to be chemically inert once it’s fully cured. It means the product resists numerous chemicals, including petroleum-based products. Manufacturer data sheets and customer support indicate that JB Weld withstands oil exposure efficiently. While explicit laboratory tests aren’t often cited, the formulation aims for high chemical resistance.
Here’s a brief breakdown of JB Weld’s resistance properties:
- Chemical Resistance:
- Resistant to petroleum products and automotive chemicals
- Designed for stability after curing
- Temperature Resistance:
- Standard JB Weld: Up to 500°F (260°C)
- Stick and quick weld versions: Up to 300°F (149°C)
Real-Life Scenarios
Users often turn to JB Weld for automotive repairs due to its proven track record. It’s commonly used on parts exposed to oil and high temperatures:
- Oil Pans:
- Successful repairs on cracked oil pans show JB Weld’s reliability.
- Users report long-term fixes that withstand oil exposure.
- Engine Components:
- Applications on various engine parts exposed to oil and heat.
- Consistent reports of successful repairs and lasting solutions.
Comparison with Other Products
When comparing JB Weld to other adhesives and epoxies, consider these factors:
Product | Chemical Resistance | Temperature Resistance | Common Uses |
---|---|---|---|
JB Weld | Resistant to petroleum and automotive chemicals | 500°F (Standard), 300°F (Stick/Quick) | Oil pans, engine components, seals |
Gorilla Epoxy | Limited resistance to petroleum products | Up to 200°F | General household repairs |
Loctite Epoxy | Resistant to some chemicals | Up to 300°F | Household, automotive repairs |
JB Weld stands out for its higher temperature resistance and broader chemical resistance, making it more suitable for automotive applications where oil exposure is a concern.
Using JB Weld gives you confidence in its ability to handle tough, oil-exposed repairs. Always follow the manufacturer’s instructions for the best results.
User Experiences
Success Stories
JB Weld is a trusted choice for oil-related repairs. Users have documented various success stories involving JB Weld, showcasing its effectiveness in critical situations.
- Oil Pan Repairs
- User Reports: Many users have sealed small cracks in oil pans, maintaining a tight seal even under high temperature and pressure conditions.
- Example: One user mentioned fixing a pinhole leak in an oil pan, allowing the vehicle to continue operation without further leakage.
- Oil Line Fixes
- User Reports: Repairs to oil lines have been successful when JB Weld was applied correctly and allowed to cure fully.
- Example: Users have noted that sealed oil lines with JB Weld showed no signs of oil seepage or weakening, even after several months of use.
- Engine Component Repairs
- User Reports: Components like valve covers and engine blocks have been repaired successfully, showcasing JB Weld’s resilience.
- Example: One example includes sealing a small crack in a valve cover. The repair held steady even through daily driving and exposure to engine oil.
Common Issues and Solutions
While JB Weld often performs well, some users have faced issues depending on how the product was applied.
- Incomplete Curing
- Issue: Improper curing can lead to weaker bonds and oil seepage.
- Solution: Ensure full curing by maintaining recommended temperature and time (15-24 hours). Verify completeness before using the repaired component.
- Surface Preparation
- Issue: Poor surface prep can diminish JB Weld’s effectiveness.
- Solution: Clean, roughen, and dry surfaces meticulously. Use alcohol to remove any remnants of oil or contaminants.
- Mixing Ratios
- Issue: Incorrect resin to hardener ratios result in improper curing.
- Solution: Mix equal parts of resin and hardener thoroughly, utilizing the full mixture within 4-6 minutes for best results.
- Excessive Heat Exposure
- Issue: Temperatures exceeding JB Weld’s threshold can degrade the bond.
- Solution: Avoid repairs in areas consistently exposed to temperatures above 550°F. For temporary fixes, regular checks and reapplication may help.
These experiences and solutions underscore the importance of following detailed preparation and application steps for successful oil-resistant repairs using JB Weld.
Conclusion
JB Weld stands out as a reliable option for oil-resistant repairs, especially in automotive contexts. Its ability to withstand significant mechanical stress and high temperatures makes it a trusted choice for fixing oil pans and engine components. Proper surface preparation and mixing are key to achieving the best results, ensuring a strong and durable bond.
User experiences and success stories further validate JB Weld’s effectiveness in maintaining tight seals under challenging conditions. By following the detailed application steps, you can confidently use JB Weld for your oil-related repair projects, knowing it will deliver dependable performance.
Frequently Asked Questions
Is JB Weld oil resistant?
Yes, JB Weld is oil resistant once fully cured, making it suitable for repairs involving oil exposure.
How long does it take for JB Weld to cure?
JB Weld sets in 4-6 hours and reaches full cure after 15-24 hours, depending on temperature.
What is the temperature resistance of JB Weld?
Standard JB Weld can endure up to 500°F (260°C). The stick and quick variants resist up to 300°F (149°C).
Can JB Weld be used to repair cracked oil pans?
Yes, JB Weld is effective for repairing cracked oil pans due to its oil resistance and durability.
How should I prepare the surface before applying JB Weld?
Clean, roughen, and dry the surface meticulously to ensure a strong bond before applying JB Weld.
What are the mixing instructions for JB Weld?
Combine equal parts of resin and hardener, and use the mixture within 4-6 minutes for best results.
Is JB Weld suitable for high-pressure applications?
Yes, JB Weld can maintain tight seals under high temperature and pressure conditions.
Can JB Weld resist both chemical and temperature exposure?
Yes, once fully cured, JB Weld is chemically inert and resistant to petroleum-based products and high temperatures.
What should I do if JB Weld does not cure properly?
Ensure proper surface preparation, correct mixing ratios, and avoid excessive heat exposure to achieve optimal results.