What Is Pressure Sensitive Adhesive: A Comprehensive Guide
Ever wondered how sticky notes cling to surfaces without any fuss? That’s the magic of pressure sensitive adhesive (PSA). Unlike traditional adhesives that require heat, water, or solvent to activate, PSA sticks when you apply light pressure. It’s incredibly versatile, used in everything from labels and tapes to medical bandages and automotive trims.
Understanding PSAs can revolutionize how you approach everyday tasks and even some DIY projects. These adhesives are designed to bond instantly and hold strong, making them indispensable in various industries. Ready to dive deeper into the world of PSAs? Let’s explore their unique properties and countless applications.
Key Takeaways
- Types of Adhesives: Pressure sensitive adhesives (PSAs) bond to surfaces when light pressure is applied, eliminating the need for heat, water, or solvents.
- Key Characteristics: PSAs are characterized by permanent tackiness and viscoelasticity, allowing them to absorb and dissipate energy efficiently.
- Versatility in Applications: PSAs are widely used in labels, tapes, medical bandages, and automotive trims due to their instant bonding and durable adhesion.
- Composition: Common materials used in PSAs include acrylate for durability, rubber for flexibility, and silicone for high-temperature stability.
- Ease of Use: PSAs are easy to apply, user-friendly, and often leave no residue upon removal. They are available in various forms such as tapes, labels, and glue dots.
What Is Pressure Sensitive Adhesive?
Pressure sensitive adhesive (PSA) is a type of adhesive that bonds to surfaces when light pressure is applied. Unlike other adhesives, it doesn’t require water, solvent, or heat to activate its bond.
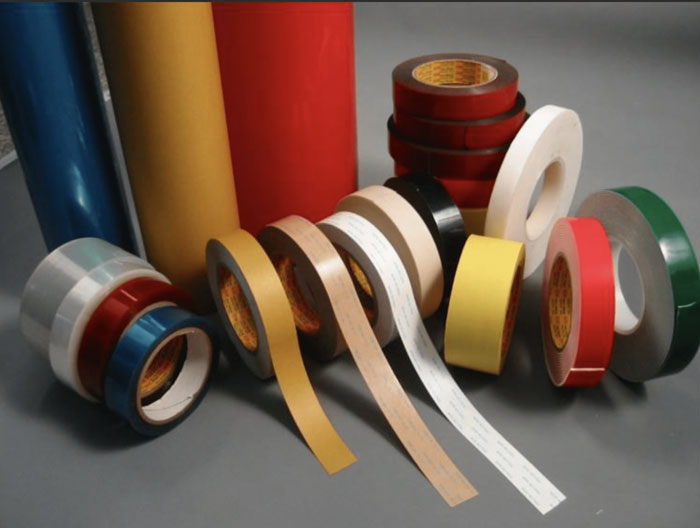
Key Characteristics
Permanent Tackiness
PSAs remain sticky at room temperature, allowing them to adhere quickly and hold firmly with minimal pressure.
Viscoelasticity
PSAs possess both viscous (fluid-like) and elastic (solid-like) properties, enabling them to absorb and dissipate energy when applied.
Composition
PSAs are made from viscoelastic polymers which are blended with tackifiers to improve their adhesive performance. Key materials include:
- Acrylate: Known for durability and resistance to environmental factors.
- Rubber (Natural or Synthetic): Provides strong initial tack and flexibility.
- Silicone: Offers high-temperature stability and chemical resistance.
Properties
- Ease of Use: Requires only light pressure to form a bond.
- Durability: Stays sticky and effective over time.
- Versatility: Suitable for a wide range of applications.
Applications
PSAs are used in numerous products due to their instant bonding capabilities. Examples include:
- Labels: Common in packaging and product information.
- Tapes: Essential in various industries for sealing and bundling.
- Medical Bandages: Provides secure yet gentle adhesion to skin.
- Automotive Trims: Used for attaching parts and reducing vibrations.
Property | Acrylate | Rubber | Silicone |
---|---|---|---|
Temperature Range | -40 to 200°F | -20 to 160°F | -100 to 500°F |
Initial Tack | Moderate | High | Low |
UV Resistance | Excellent | Poor | Excellent |
Chemical Resistance | Good | Fair | Excellent |
Understanding pressure sensitive adhesives can help you choose the right type for your needs, whether for DIY projects or professional applications. Consider the specific properties and applications to maximize the effectiveness of PSAs in your projects.
How Do PSAs Work?
Understanding how PSAs work can enhance your usage of products like stickers, labels, and tapes. PSAs form bonds when applied with pressure. No heat, water, or solvents are needed. Let’s examine the factors that make this possible:
Key Characteristics of PSAs
- Permanent Tackiness: PSAs remain sticky over time.
- Viscoelasticity: The adhesive behaves like both a solid and a liquid, enabling it to spread and conform to surfaces.
- Composition: Made from viscoelastic polymers combined with tackifiers, including acrylate, rubber, and silicone.
Mechanism of Bond Formation
- Surface Contact: When you press the adhesive against a surface, the tacky material conforms to the surface contours, increasing contact area.
- Wet-Out: The adhesive flows into microscopic irregularities of the surface, creating more points of contact.
- Adhesion Forces: Physical interactions, such as van der Waals forces, strengthen the bond between the adhesive and the substrate.
- Cohesion Strength: The internal strength of the adhesive resists separation.
Factors Influencing PSA Bond Strength
- Surface Cleanliness: Dirt and oils can weaken the bond. Clean surfaces enhance adhesion.
- Application Pressure: Higher pressure increases surface contact and improves bond strength.
- Application Temperature: Optimal temperatures ensure the best adhesive flow and bond formation.
- Material Compatibility: Different adhesives work better on certain materials. Match PSA to the substrate for optimal results.
Types of PSAs
- Permanent PSAs: Used for applications requiring long-term adhesion, such as automotive trims and industrial tapes.
- Removable PSAs: Ideal for temporary applications where removal without residue is important, such as masking tapes and removable labels.
- Labels: Barcodes, shipping labels, and product labels.
- Tapes: Electrical tapes, medical bandages, and duct tapes.
- Stickers: Decorative stickers, bumper stickers, and office supply stickers.
- Industrial: Automotive trims, appliance assembly, and medical device assembly.
By grasping these details, you can make better-informed decisions about using PSAs in various projects, maximizing their effectiveness and longevity.
Types of Pressure-Sensitive Adhesives
Understanding the various types of pressure-sensitive adhesives (PSAs) helps you choose the right one for your specific needs. The main types include Rubber-Based Adhesives and Acrylic-Based Adhesives.
Adhesive Tape
Adhesive tape is one of the most common forms of PSAs. These tapes are designed for convenience, offering both strong adhesion and easy removability without leaving residue. They are used in diverse applications, from simple household tasks to complex industrial uses.
- Packing Tape: Strong adhesion, ideal for sealing boxes and parcels.
- Masking Tape: Easy removability, suitable for painting and surface protection.
- Electrical Tape: Insulative properties, used for electrical wiring and insulation.
Single-Faced Product
Single-faced products have adhesive on one side only. They offer a straightforward application process and are frequently used for attaching items where only one surface needs to be bonded.
- Duct Tape: Strong, versatile, used for repairs and construction.
- Medical Tapes: Safe for skin contact, used in medical settings for wound care.
- Label Stickers: Permanent or removable, used for product identification and organization.
Double-Faced Product
Double-faced products have adhesive on both sides, making them ideal for applications requiring a strong, hidden bond between two surfaces. These are commonly used in mounting and laminating tasks.
- Carpet Tape: Provides secure placement, used for keeping carpets in place.
- Mounting Tape: High-strength, used for attaching objects to walls and surfaces.
- Photo-safe Tape: Acid-free, used in scrapbooking and photo albums.
Transfer Tape
Transfer tape is a unique type of PSA where the adhesive is provided on a liner, with no carrier backing. This design allows for a clean and precise transfer of the adhesive to a new surface.
- Graphics Tape: Used in sign making and graphic design for precise adhesive placement.
- VHB Tape: Industrial-grade, providing strong adhesion for heavy-duty applications.
- Splicing Tape: Used in paper and film industries for seamless joining and repairs.
PSA Type | Key Properties | Common Uses |
---|---|---|
Rubber-Based Adhesives | High tack, good shear properties, flexible | Packaging, labeling, repairs |
Acrylic-Based Adhesives | Long-term stability, UV resistance, high-temperature performance | Outdoor applications, automotive, medical uses |
Choosing the right PSA involves considering the specific requirements of your project, such as adhesion strength, surface compatibility, and environmental resistance.
What Materials Are PSAs Made Of?
Pressure-sensitive adhesives (PSAs) consist of various materials designed to meet specific performance criteria. Each material brings unique properties to the adhesives, making them suitable for different applications. This section delves into the key materials used in PSAs.
Rubber/Resin
Rubber-based PSAs combine natural or synthetic rubber with tackifying resins. These adhesives are cost-effective and offer excellent initial tack.
- Properties:
- Quick adhesion at low pressure
- Cost-effective
- Susceptible to heat degradation
- Applications:
- Packaging tapes
- Labels
- General-purpose bonding
Acrylic
Acrylic-based PSAs use polymers derived from acrylate monomers. They are known for their durability and resistance to environmental factors.
- Properties:
- High UV, heat, and chemical resistance
- Long-lasting adhesion
- Clarity and transparency
- Applications:
- Outdoor labels and signs
- Automotive trims
- Medical tapes
Silicone
Silicone-based PSAs are ideal for high-temperature applications and surfaces with low surface energy.
- Properties:
- Outstanding high-temperature resistance
- Excellent adherence to difficult substrates (e.g., silicone release liners)
- Biocompatibility
- Applications:
- Medical bandages
- High-performance automotive components
- Aerospace applications
Here’s a quick comparison of the key materials used in PSAs:
Material | Properties | Common Applications |
---|---|---|
Rubber/Resin | Quick adhesion, cost-effective, heat-sensitive | Packaging tapes, Labels, General-purpose bonding |
Acrylic | High UV/heat resistance, durable, transparent | Outdoor labels, Automotive trims, Medical tapes |
Silicone | High-temperature resistance, adheres to difficult substrates, biocompatible | Medical bandages, High-performance automotive parts, Aerospace components |
Each material in PSAs offers specific advantages, making PSAs highly versatile and effective in various industries.
How Are PSAs Made?
Pressure-sensitive adhesives (PSAs) are produced using several manufacturing methods, each catering to different application requirements. Here, you’ll find an overview of the common methods used to create PSAs.
Solvent
This method involves dissolving adhesive ingredients in a solvent. The process includes:
- Preparation: Ingredients like polymers and tackifiers are dissolved in organic solvents.
- Application: The adhesive mixture is coated onto a substrate.
- Evaporation: Solvent is evaporated, leaving behind pure adhesive.
Solvent-based PSAs are known for their strong adhesion and versatility in various industries but can be labor-intensive and costly.
Water-Based
In water-based production, ingredients are dispersed in water instead of solvents. The steps are:
- Preparation: Polymers and additives are mixed in water to form a stable dispersion.
- Application: The mixture is coated onto substrates like paper or film.
- Drying: Water is evaporated through heat or air drying, leaving the adhesive layer.
Water-based PSAs provide a more environmentally friendly alternative due to lower volatile organic compound (VOC) emissions.
Hot-Melt
Hot-melt PSAs are produced by heating the adhesive until it becomes liquid and then applying it to a substrate. The process is:
- Preparation: Adhesive components are mixed and heated to 160-180°C.
- Application: The molten adhesive is applied to the substrate.
- Cooling: Adhesive solidifies upon cooling, forming a strong bond.
Hot-melt PSAs offer rapid curing times and are widely used in packaging and automotive industries.
UV-Curable
UV-curable PSAs use ultraviolet light to initiate curing. The process involves:
- Preparation: Adhesive mixture contains photoinitiators that react to UV light.
- Application: Coating the adhesive on substrates.
- Curing: Exposing the adhesive layer to UV light for quick setting.
UV-curable PSAs are ideal for precision applications, offering rapid curing and strong adhesion.
Method | Solvent-Based | Water-Based | Hot-Melt | UV-Curable |
---|---|---|---|---|
Preparation | Dissolved in solvents | Dispersed in water | Heated to a liquid state | Contains photoinitiators |
Application | Coated and evaporated | Coated and dried | Coated in molten form | Coated and UV-exposed |
Environmental Impact | High VOC emissions | Low VOC emissions | Minimal emissions | No emissions |
Curing Time | Relatively slow | Variable | Rapid | Instantaneous |
Common Uses | Industrial, automotive | Labels, tapes | Packaging, automotive | Medical, electronics |
Understanding the different methods of PSA production helps you choose the right type for your needs, based on environmental concerns, curing times, and specific applications.
Applications of Pressure-Sensitive Adhesives
Pressure-sensitive adhesives (PSAs) find applications across various industries due to their versatility and ease of use. The following sections detail some of the most common and important applications.
Labeling
- Product Labels: PSAs are crucial in labeling consumer products. They’re widely used for food packaging, beverages, and household items due to their strong adhesion and durability.
- Barcode Labels: PSAs ensure quick, reliable attachment of barcode labels to products, aiding in inventory management and tracking.
Tapes
- Packaging Tape: PSAs provide the necessary adhesion for securing boxes and packages, making them essential in shipping and logistics.
- Masking Tape: Used in painting and surface protection, masking tape with PSAs offers easy removal and leaves no residue.
- Electrical Tape: PSAs in electrical tape provide insulation and protection for wiring and electrical components.
Medical
- Bandages and Dressings: PSAs are used in medical bandages and dressings to offer secure attachment to the skin while allowing for easy removal without skin irritation.
- Medical Devices: Adhesive patches and sensors use PSAs for reliable skin adhesion in wearable medical devices.
Automotive
- Trim and Emblems: PSAs are essential in attaching trims, emblems, and badges to vehicles, offering strong bonding that withstands environmental stress.
- Interior Panels: Used for securing interior panels and components, ensuring they stay in place under varying conditions.
Electronics
- Screen Protectors: PSAs are used in screen protectors for smartphones and tablets, providing bubble-free application and strong adhesion.
- Component Mounting: PSAs help in mounting components within electronic devices, providing shock absorption and stability.
Industrial
- Assembly: PSAs play a significant role in assembling parts where traditional methods (screws or bolts) aren’t feasible. They’re useful in lightweight assembly and quick repairs.
- Spacer Tapes: In construction, spacer tapes with PSAs are used to maintain uniform spacing in glazing applications, ensuring proper installation.
Home and Office
- Sticky Notes and Labels: Commonly found in homes and offices, sticky notes and labels use PSAs to provide temporary adhesion for notes and reminders.
- Decorative Hooks: PSAs on decorative hooks allow for easy installation and removal without damaging walls.
Market Segments Utilization
Market Segment | Example Applications | Key Attributes |
---|---|---|
Consumer Goods | Food packaging, beverage labeling, household item labels | Strong adhesion, durability, moisture resistance |
Transportation | Automotive trims, emblems, interior panels | Environmental stress resistance, strong bonding |
Healthcare | Medical bandages, dressings, adhesive patches | Skin-friendly, hypoallergenic, easy removal |
Electronics | Screen protectors, component mounting, wearable sensors | Shock absorption, bubble-free application |
Industrial | Assembly, spacer tapes, quick repairs | Lightweight assembly, ease of use |
Summary
PSAs demonstrate a wide range of applications from labeling consumer goods to industrial assembly. Their versatile nature, combined with varying adhesive strengths and material compatibilities, makes them integral across multiple sectors. By understanding the different uses and selecting the right type of PSA, you can improve efficiency and effectiveness in many projects, whether professional or DIY.
Advantages of Pressure-Sensitive Adhesives
Pressure-sensitive adhesives (PSAs) offer numerous benefits that make them ideal for various applications. These advantages highlight why industries rely on PSAs for efficient bonding solutions.
Ease of Use
- No Activation Required: PSAs form bonds without the need for heat, water, or solvents, making them simple to apply. You can install a PSA by just applying pressure.
- User-Friendly: These adhesives come in ready-to-use forms like tapes and labels, allowing for straightforward use in everyday tasks and industrial applications.
Versatility
- Material Compatibility: PSAs adhere to diverse surfaces, including glass, metals, plastics, and fabrics. For instance, they bond well with automotive trims and electronic components.
- Variety of Forms: Available as tapes, labels, glue dots, and stickers, PSAs meet different needs across various sectors.
Instant Bonding
- Immediate Grip: PSAs provide instant adhesion with the application of pressure, making them excellent for time-sensitive projects.
Strong Bonding
- Durable: The bond strength of PSAs increases with the amount of pressure applied. High surface energy materials also enhance bonding performance.
- Reliable: PSAs maintain integrity under stress and temperature variations, making them reliable for outdoor and high-heat applications.
Clean Application
- Residue-Free Removal: Many PSAs offer clean removal options, leaving no sticky residue behind. This feature is advantageous in applications like tapes for home decor or labeling electronics.
- No Mess: Unlike liquid adhesives, PSAs avoid spillages and drying time, facilitating a more efficient workflow.
Flexibility
- Adjustable Bonding: PSAs range from permanent to removable, offering flexibility based on your project requirements. For example, sticky notes use repositionable PSAs while industrial tapes use permanent ones.
- Conformability: These adhesives conform to irregular surfaces, ensuring proper adhesion on curved or textured materials.
Cost-Effective
- Reduced Downtime: Instant bonding and minimal preparation save time and labor costs. Companies benefit from the faster application in manufacturing processes.
- Lower Waste: The ready-to-use nature of PSAs minimizes waste compared to traditional adhesives that may need mixing and precise measurements.
Environmental Considerations
- Low VOC: Many PSAs are designed with low volatile organic compound (VOC) emissions, making them more environmentally friendly.
- Sustainable Options: Alternatives like water-based PSAs provide more sustainable choices compared to solvent-based adhesives.
Feature | Advantages |
---|---|
Ease of Use | No activation required, User-friendly forms |
Versatility | Adheres to multiple materials, Available in various forms |
Instant Bonding | Immediate grip upon application |
Strong Bonding | Durable adhesion, Maintains bond under stress |
Clean Application | Residue-free removal, No mess with liquid adhesives |
Flexibility | Adjustable bonding from temporary to permanent, Conforms to irregular surfaces |
Cost-Effective | Saves time and labor costs, Minimizes waste |
Environmental | Low VOC emissions, Water-based and sustainable alternatives |
Understanding these advantages, you can better appreciate the efficiency and effectiveness PSAs offer for both everyday tasks and specialized industrial applications.
Conclusion
Pressure-sensitive adhesives (PSAs) offer a versatile and efficient solution for bonding needs across various industries. Their ability to adhere instantly without the need for heat, water, or solvents makes them indispensable in everyday tasks and specialized applications alike. From labels and tapes to medical and automotive uses, PSAs provide strong, reliable bonds that can withstand different conditions.
Understanding the properties, types, and manufacturing methods of PSAs enables you to select the right adhesive for your specific projects. Whether you’re working on a simple DIY project or a complex industrial application, PSAs deliver the performance and reliability you need. By leveraging the unique advantages of PSAs, you can enhance productivity and achieve superior results in your bonding tasks.
Frequently Asked Questions
What are pressure-sensitive adhesives (PSAs)?
Pressure-sensitive adhesives (PSAs) are adhesives that bond with surfaces upon the application of light pressure. They do not require heat, water, or solvents to activate and are used in products like sticky notes, labels, and tapes.
How do pressure-sensitive adhesives work?
PSAs bond to surfaces through a process of surface contact, wet-out, and adhesion forces. Factors like surface cleanliness, application pressure, and temperature influence their bond strength.
What are the types of pressure-sensitive adhesives?
PSAs include rubber-based and acrylic-based adhesives, each with unique properties. Rubber-based PSAs adhere quickly and are cost-effective, while acrylic-based PSAs offer durability and environmental resistance.
What is the difference between permanent and removable PSAs?
Permanent PSAs form strong, lasting bonds suitable for applications like automotive trims. Removable PSAs can be removed cleanly without damaging surfaces, making them ideal for temporary uses like sticky notes.
What materials are used to make PSAs?
PSAs are made from viscoelastic polymers blended with tackifiers such as acrylate, rubber, and silicone. Each material provides specific properties like environmental resistance or high-temperature performance.
How are pressure-sensitive adhesives manufactured?
PSAs are produced through methods like solvent-based, water-based, hot-melt, and UV-curable processes. Each method has different preparation times, curing conditions, and environmental impacts.
Where are PSAs commonly used?
PSAs are used in a variety of industries, including labeling, packaging, electronics, medical applications, automotive trims, and household items like sticky notes.
Are PSAs environmentally friendly?
Some PSAs are designed to be more environmentally friendly. For example, water-based PSAs have lower VOC emissions compared to solvent-based adhesives.
What are the advantages of using PSAs?
Advantages of PSAs include ease of use, versatility, instant bonding, strong hold, clean application, flexibility, cost-effectiveness, and suitability for various environmental conditions.
Can PSAs be used in high-temperature applications?
Yes, certain PSAs, like silicone-based adhesives, excel in high-temperature applications and are used in fields like medical and aerospace industries.