Sikaflex 252 vs 221: A Detailed Comparison for Your Projects
When you’re tackling a project that requires strong bonding and sealing, choosing the right adhesive is crucial. Sikaflex 252 and Sikaflex 221 are two popular options, but how do you decide which one suits your needs best? Both products offer unique benefits and are designed for different applications, making the decision a bit more complex.
In this text, you’ll discover the key differences between Sikaflex 252 and 221, helping you make an informed choice. Whether you’re working on a vehicle, boat, or construction project, understanding these distinctions will ensure you achieve the best results. Let’s jump into the specifics so you can confidently pick the right adhesive for your next project.
Key Takeaways
- Purpose and Strength: Sikaflex 252 is designed for high-strength bonding applications, while Sikaflex 221 is suitable for general sealing and bonding tasks requiring less mechanical strength.
- Flexibility and Elasticity: Sikaflex 221 offers superior flexibility and elasticity, making it ideal for dynamic environments with movement and vibration. In contrast, Sikaflex 252 is more rigid, suitable for applications demanding minimal flexibility and higher tensile strength.
- Application Areas: Sikaflex 221 is commonly used in automotive and construction industries for bonding materials like metal, glass, and plastics. Sikaflex 252 is preferred for heavy-duty bonding and structural areas needing high mechanical strength.
- Performance Features: Sikaflex 252 provides higher tensile strength and excellent durability, making it suitable for structural bonding. Sikaflex 221 is known for its versatility and user-friendly application, fitting general-purpose bonding and sealing needs.
- Safety and Handling: Both Sikaflex 252 and 221 require precautions for respiratory and skin sensitization, emphasizing the importance of protective gear and proper ventilation during use.
- User Feedback: Sikaflex 252 is praised for its strong, durable bonds in heavy-duty applications, while Sikaflex 221 is valued for its flexibility and ease of use in general bonding and sealing tasks.
Overview Of Sikaflex 252 And 221
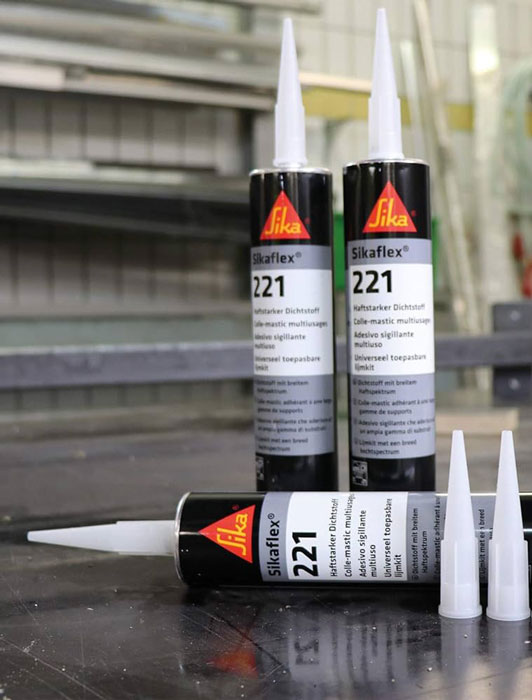
Key Differences and Applications
Purpose and Strength
- Sikaflex 221: Primarily an adhesive sealant, Sikaflex 221 is suitable for sealing and bonding tasks where moderate mechanical strength is needed. It’s ideal for general sealing and bonding of different materials, known for its flexibility and resistance to weathering.
- Sikaflex 252: Designed for higher strength bonding applications, Sikaflex 252 has a higher tensile strength than Sikaflex 221. It’s more appropriate for tasks requiring stronger bonds.
- Sikaflex 221: Ideal for applications needing a flexible seal. Common uses include:
- Automotive and construction industries
- Sealing joints
- Bonding materials like metal, glass, and plastics
- RVs, trucks, and fiberglass applications
- Sikaflex 252: Suitable for scenarios requiring higher bond strength. Common applications include:
- Heavy-duty bonding
- Structural areas needing high tensile strength
Key Features
When comparing Sikaflex 252 and Sikaflex 221, understanding their key features helps determine the best choice for your specific needs.
Strength And Durability
-
Sikaflex 252:
- Tensile Strength: Higher than Sikaflex 221, making it suitable for applications requiring robust bonding.
- Durability: Known for excellent long-term durability, especially in structural areas that demand high strength.
-
Sikaflex 221:
- Tensile Strength: Lower yet sufficient for many applications, suitable for bonding dissimilar metals.
- Durability: Proven to work effectively in various environments over the years, including metal, glass, and plastics.
Flexibility And Elasticity
-
Sikaflex 221:
- Elasticity: Superior elasticity, making it ideal for sealing and bonding in dynamic environments with movement and vibration.
- Flexibility: Highly flexible, preferred in automotive and construction industries where flexibility is key.
-
Sikaflex 252:
- Elasticity: While elastic, it is less flexible compared to Sikaflex 221.
- Flexibility: More rigid, suitable for applications where stiffness is needed and minor flexibility suffices.
Feature | Sikaflex 252 | Sikaflex 221 |
---|---|---|
Tensile Strength | Higher, suitable for high-strength bonding | Lower, adequate for general applications |
Durability | Excellent, ideal for structural areas | Proven effective in various environments |
Elasticity | Less flexible | Superior, ideal for dynamic environments |
Flexibility | More rigid, suitable for stiff applications | Highly flexible, preferred in automotive/construction |
By examining these features closely, you can make an well-informed choice on whether Sikaflex 252 or Sikaflex 221 is more appropriate for your project.
Application Areas
Common Uses For Sikaflex 252
Sikaflex 252 stands out in applications requiring strong bonding and high tensile strength. Designed for specific industrial needs, it excels in various demanding environments.
- Higher Strength Bonding: Utilized in scenarios where high tensile strength and robust bonds are critical, Sikaflex 252 is a go-to adhesive. It ensures reliable bonding for heavy-duty applications.
- Metal to Metal and Dissimilar Materials: Perfect for bonding different materials, Sikaflex 252 is commonly used to bond aluminum to fiberglass and other dissimilar materials. This versatility makes it ideal for manufacturing and maintenance processes.
- Structural Bonding: Selected for its proficiency in structural bonding, where high mechanical strength is paramount. This adhesive is suitable for construction tasks that require strong support and durability.
Common Uses For Sikaflex 221
Sikaflex 221 is versatile and offers excellent adhesion and flexibility. It fits well in general bonding and sealing tasks where moderate mechanical strength suffices.
- General Sealing and Bonding: Functions effectively in general sealing and bonding tasks, making it suitable for multiple industries, including automotive and construction.
- Automotive Applications: Frequently used in the automotive industry for bonding materials such as metal, glass, and plastics. Sikaflex 221’s flexibility ensures it withstands dynamic movements and vibrations.
- Construction Tasks: Commonly applied in construction for sealing joints and bonding different materials. It adapts well to varied environmental conditions, providing dependable performance.
Property | Sikaflex 252 | Sikaflex 221 |
---|---|---|
Primary Use | High-strength bonding applications | General sealing and bonding |
Tensile Strength | Higher | Moderate |
Flexibility | Less flexible | Highly flexible |
Common Materials | Metal, fiberglass, dissimilar materials | Metal, glass, plastics |
Industry Usage | Marine, industrial, vehicle repairs | Automotive, construction |
Sikaflex 252 and Sikaflex 221 cater to different needs within the bonding and sealing spectrum. By understanding their unique properties and possible applications, you can choose the adhesive that best suits your project requirements.
Comparison Of Performance
When choosing between Sikaflex 252 and Sikaflex 221, understanding their performance differences is crucial. Below, we break down the key aspects to help you make an well-informed choice.
Adhesion Strength
Sikaflex 221:
- Offers moderate mechanical strength
- Suitable for general-purpose bonding and sealing
- Ideal for materials like metal, glass, and plastics
Sikaflex 252:
- Provides higher mechanical strength compared to Sikaflex 221
- Better suited for applications requiring stronger bonds and higher tensile strength
- Often used for structural bonding in heavy-duty applications
Weather Resistance
Both Sikaflex 221 and 252:
- Known for excellent weather resistance
- Perform well in a variety of environmental conditions
- Suitable for both indoor and outdoor applications
Ease Of Application
Sikaflex 221:
- Versatile and user-friendly
- Easily applied with a standard caulking gun
- Cures at room temperature, simplifying the application process
- Popular choice for automotive, construction, and industrial projects
Sikaflex 252:
- Requires more careful preparation due to its stronger bonding properties
- May need specific surface treatments to achieve optimal adhesion
- Also applied with a standard caulking gun but may benefit from professional application for best results in structural applications
Feature | Sikaflex 221 | Sikaflex 252 |
---|---|---|
Mechanical Strength | Moderate | High |
Tensile Strength | Suitable for general purposes | Suitable for structural bonding |
Weather Resistance | Excellent | Excellent |
Application Versatility | High | High but requires surface treatment |
Common Uses | Automotive, construction, industrial | Heavy-duty, structural bonding |
By closely analyzing these performance aspects, you can choose the adhesive that best suits your project needs—whether it’s a general-purpose bonding task with Sikaflex 221 or a heavy-duty structural application with Sikaflex 252.
Safety And Handling Precautions
When dealing with Sikaflex 252 and Sikaflex 221, it’s essential to follow specific safety and handling precautions due to their polyurethane-based composition. Understanding these precautions ensures you maintain a safe working environment.
Respiratory Sensitization and Skin Sensitization
- Respiratory Sensitization: Sikaflex 252 and Sikaflex 221 can cause respiratory sensitization, classified under Category 1. This means that inhalation of the product can trigger allergic reactions in the respiratory system.
- Skin Sensitization: Both products can also cause skin sensitization, classified under Category 1. Direct contact with the skin can result in allergic reactions or dermatitis.
Carcinogenicity
- Inhalation Hazard: Both Sikaflex 252 and Sikaflex 221 are classified as Category 1A for carcinogenicity by inhalation. Prolonged or repeated inhalation exposure could potentially lead to cancer. Always handle these adhesives in well-ventilated areas or use appropriate respiratory protection.
Specific Target Organ Toxicity
- Organ Damage: Both adhesives are classified under Category 2 for specific target organ toxicity. This classification means they can cause damage to organs through prolonged or repeated exposure. Ensure you minimize frequent exposure and use suitable protective equipment to reduce risk.
Recommended Safety Measures
To mitigate the risks associated with Sikaflex 252 and Sikaflex 221, adhere to the following safety measures:
- Wear protective gloves and clothing to prevent skin contact.
- Use safety goggles to protect your eyes from splashes.
- Use respirators or work in well-ventilated areas to avoid inhalation of fumes.
- Wash hands and any skin exposed to the adhesive thoroughly after handling.
Handling Instructions
Proper handling of Sikaflex 252 and Sikaflex 221 enhances safety and product performance:
- Storage: Store in a cool, dry place away from direct sunlight. Ideal storage temperature ranges are specified on the product packaging.
- Application: Follow the manufacturer’s instructions for surface preparation and adhesion techniques. For Sikaflex 252, ensure surfaces are clean and roughened for optimal bond strength.
- Disposal: Dispose of any unused product and packaging according to local regulations. Avoid releasing the adhesive into the environment.
Safety Comparisons
Here is a comparison of the key safety classifications for Sikaflex 252 and Sikaflex 221:
Safety Aspect | Sikaflex 252 | Sikaflex 221 |
---|---|---|
Respiratory Sensitization | Category 1 | Category 1 |
Skin Sensitization | Category 1 | Category 1 |
Carcinogenicity by Inhalation | Category 1A | Category 1A |
Specific Target Organ Toxicity | Category 2 | Category 2 |
By diligently adhering to these safety and handling precautions, you can safely use Sikaflex 252 and Sikaflex 221 for your bonding and sealing needs while minimizing health risks.
User Reviews And Feedback
Bonding Strength
Sikaflex 252: Many users highlight its superior bonding strength. It’s frequently chosen for applications requiring robust and long-lasting bonds. For instance, users involved in heavy-duty vehicle assembly and structural bonding find Sikaflex 252 indispensable due to its higher tensile strength.
Sikaflex 221: Users appreciate its reliability for general bonding and sealing tasks. Though it has a lower tensile strength compared to 252, it’s still favored in situations where moderate strength suffices, such as automotive restorations and general construction.
Flexibility and Elasticity
Sikaflex 221: Renowned for its flexibility, it remains a preferred choice for projects involving vibration and movement. Users working on dynamic applications, like bonding panels in classic cars, find Sikaflex 221’s elasticity ensures durability over time.
Sikaflex 252: While it does offer some flexibility, it’s stiffer than 221. Users needing minimal movement and maximum bond integrity opt for 252, especially in heavy-duty structural applications.
Usage Scenarios
Sikaflex 221:
- Sealing and Bonding: Ideal for diverse materials such as metals, glass, and plastics. Frequently employed in automotive restorations and exterior joint sealings.
- Restorations: Users have successfully utilized it for bonding bonnets on classic cars, highlighting its adaptability.
Sikaflex 252:
- Structural Bonding: Perfect for applications demanding high tensile strength and rigidity. Used extensively in vehicle assembly and construction.
- Durable Bonds: Preferred for tasks like bonding metal frameworks, where a strong, long-lasting hold is critical.
User Feedback on Performance
Attribute | Sikaflex 252 | Sikaflex 221 |
---|---|---|
Bonding Strength | Higher tensile strength, suitable for heavy-duty applications | Moderate, suitable for general purposes |
Flexibility | Lower elasticity, suited for rigid bonds | High flexibility, ideal for dynamic applications |
Ease of Use | Requires surface preparation | User-friendly, easier application |
Weather Resistance | Excellent for harsh conditions | Reliable, suitable for varied environments |
Safety and Handling
Important Considerations:
- Sikaflex 252: Requires careful surface preparation. Users report needing to follow detailed safety guidelines due to its stronger chemical properties.
- Sikaflex 221: Easier to handle but still necessitates basic safety measures. Users appreciate the fewer preparation steps and straightforward application process.
Recommended Safety Measures:
- Protective Gear: Wear appropriate safety gear to shield skin and eyes.
- Ventilation: Ensure proper ventilation to avoid inhaling fumes from the polyurethane components.
Summary/Action Point
Choosing between Sikaflex 252 and 221 depends on your specific application needs. For projects demanding high strength and rigidity, Sikaflex 252 is the preferred choice. For tasks requiring flexibility and ease of use, Sikaflex 221 stands out. Evaluate your project’s requirements to select the most suitable adhesive.
Conclusion
Choosing between Sikaflex 252 and Sikaflex 221 eventually hinges on your specific project needs. If your task demands high strength and rigidity, Sikaflex 252 is your go-to adhesive. Its superior tensile strength and durability make it perfect for heavy-duty and structural applications.
On the other hand, Sikaflex 221 excels in flexibility and ease of use. It’s ideal for general bonding and sealing tasks, especially in dynamic environments where movement and vibration are factors. Its versatility makes it a reliable choice for various materials and conditions.
Both products offer excellent weather resistance and are suitable for both indoor and outdoor applications. Remember to follow safety precautions when handling these adhesives to ensure a safe and effective application process.
Frequently Asked Questions
What are the main differences between Sikaflex 252 and Sikaflex 221?
Sikaflex 252 is designed for high strength bonding in heavy-duty and structural applications, while Sikaflex 221 is suited for general sealing and bonding tasks with moderate mechanical strength. Sikaflex 252 offers higher tensile strength and durability, whereas Sikaflex 221 excels in flexibility and elasticity.
Which Sikaflex is best for dynamic environments with movement?
Sikaflex 221 is best for dynamic environments with movement and vibration due to its superior flexibility and elasticity, making it ideal for automotive and general construction uses.
Can Sikaflex 252 be used for structural bonding?
Yes, Sikaflex 252 is perfect for structural bonding applications, offering high tensile strength and excellent long-term durability. It’s commonly used for bonding metals and dissimilar materials in robust construction tasks.
Are both Sikaflex 252 and Sikaflex 221 weather-resistant?
Yes, both Sikaflex 252 and Sikaflex 221 provide excellent weather resistance, making them suitable for both indoor and outdoor applications.
Is Sikaflex 221 easy to apply?
Yes, Sikaflex 221 is user-friendly and straightforward to apply, making it a popular choice for general-purpose bonding and sealing tasks.
What safety precautions should I take when using Sikaflex adhesives?
When using Sikaflex adhesives, wear protective gear, ensure proper ventilation, and follow handling instructions for storage and disposal. These steps help minimize risks of respiratory and skin sensitization, as well as other health hazards.
Can Sikaflex 221 be removed after application?
Uncured Sikaflex 221 can be removed from tools and surfaces using Sika Remover-208 or another suitable solvent. Removal after curing is more difficult and may require mechanical methods.
Is Sikaflex 252 waterproof?
Yes, Sikaflex 252 is waterproof once cured, making it effective for applications in the caravan, camping industry, and where strong and waterproof bonding is required.
How does Sikaflex 252 compare in tensile strength to Sikaflex 221?
Sikaflex 252 has a higher tensile strength than Sikaflex 221, making it better suited for heavy-duty and structural bonding applications that require strong, durable bonds.