How Long Does Rubber Cement Take to Dry: Key Factors and Tips
Ever found yourself in the middle of a project, wondering just how long it’ll take for that rubber cement to dry? You’re not alone. Whether you’re working on a craft, repairing a shoe, or tackling a DIY project, knowing the drying time can make all the difference in achieving a smooth finish.
Rubber cement is a versatile adhesive, but its drying time can vary based on several factors. Temperature, humidity, and the thickness of the application all play a role. Understanding these factors will help you plan better and avoid any sticky situations. Let’s jump into what you need to know to ensure your project goes off without a hitch.
Key Takeaways
- Drying Time Factors: Rubber cement drying time varies based on temperature, humidity, and application thickness. Warm, dry conditions speed up the process, while cold, humid conditions slow it down.
- Application Thickness: Thin layers of rubber cement dry faster, typically within 15 minutes to 1 hour, whereas thicker applications can take several hours or even up to 24 hours.
- Ventilation Importance: Proper ventilation accelerates the drying of rubber cement. Working in well-ventilated areas and using fans can help the solvent evaporate more quickly.
- Types of Rubber Cement: Different types of rubber cement (quick-drying, standard, and industrial) have varying drying times. Always check the manufacturer’s instructions for precise drying times.
- Common Issues: Extended drying times and incomplete bonding can occur due to environmental conditions and improper application. Ensuring clean surfaces and evenly applied thin layers can mitigate these problems.
- Optimal Conditions: For efficient drying, maintain a temperature range of 65°F-85°F and low humidity levels below 50%. Adequate air circulation also plays a crucial role in reducing drying time.
Understanding Rubber Cement
Rubber cement is a popular adhesive solution used for various applications, primarily due to its versatility and ease of use.
What is Rubber Cement?
Rubber cement is an adhesive made from unvulcanized rubber dissolved in a solvent. This composition allows it to bond rubber-to-rubber surfaces effectively and can also be used on materials like paper.
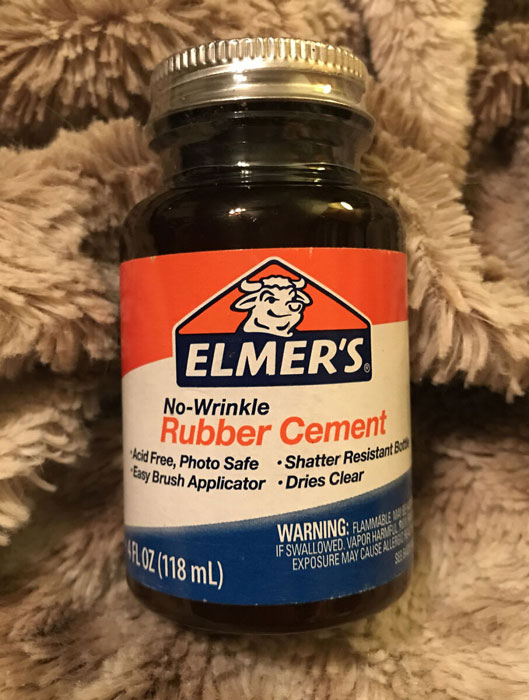
Key Components:
- Rubber: Pulverized natural or synthetic rubber. Natural rubber originates from the Hevea brasiliensis tree, while synthetic variations include neoprene and latex.
- Solvent: Usually hexane or heptane, with additional substances like isopropyl alcohol or ethyl alcohol.
Rubber cement’s ability to form a strong, flexible bond prevents materials from becoming brittle and breaking.
- Standard Rubber Cement: Commonly used for general purposes like mounting photographs or repairing rubber items. Its application is straightforward, making it the go-to choice for many household and craft projects.
These properties make rubber cement a versatile and useful tool in various settings, from DIY crafts to professional repairs.
Factors Affecting Drying Time
Several factors affect the drying time of rubber cement, which can influence how quickly you can proceed with your project. Understanding these factors helps you better plan and execute your tasks.
Application Thickness
Thin Coats: Rubber cement dries faster when applied in thin layers. Thin coats can become tacky within 15-20 minutes. Typically, they are fully dry within 15 minutes to an hour, depending on the specific product and environmental conditions.
Thick Coats: Thicker applications take much longer to dry. These may require several hours or even extend up to 24 hours to fully set. The increased volume of material slows down the evaporation process.
Environmental Conditions
Temperature and Humidity: Higher temperatures and dry conditions accelerate the drying process. In hot, dry weather, rubber cement can set in minutes. Conversely, cold and humid conditions slow down drying, leading to a prolonged setting time.
Air Circulation: Adequate air circulation facilitates quicker drying. When the workspace is well-ventilated, the rubber cement dries faster as the moving air aids in the evaporation of solvents.
Type of Rubber Cement
General-Purpose Rubber Cement: This type is designed for everyday tasks and usually has a moderate drying time. Typical products in this category dry within the standard 15-20 minutes for thin coats and several hours for thicker applications.
Specialty Rubber Cement: Some rubber cements are formulated for specific applications, like industrial use or repair work, and may have different drying times. Always check the manufacturer’s instructions for precise drying times.
Application Thickness | Environmental Condition | Drying Time (Thin Coat) | Drying Time (Thick Coat) |
---|---|---|---|
Thin | Hot and Dry | 15 minutes – 1 hour | 1-2 hours |
Thick | Cold and Humid | 2-3 hours | Up to 24 hours |
Consider these factors when working with rubber cement to achieve the best results. Properly planning your application can prevent delays and ensure a strong, lasting bond.
Average Drying Times
Understanding the average drying times of rubber cement is crucial for effective project planning. Drying times vary based on the type of rubber cement you’re using. Below are detailed drying times for different types.
Quick-Drying Rubber Cement
Quick-drying rubber cement is designed for speed. It becomes touch-dry relatively fast, making it ideal for time-sensitive projects.
- Dries to the touch: 5-10 minutes
- Full bonding strength: 30 minutes to 1 hour
Standard Rubber Cement
Standard rubber cement offers moderate drying times and is suitable for most general-purpose tasks.
- Dries to the touch: 10-15 minutes
- Optimal adhesion: 1-2 hours before handling bonded materials
Industrial Rubber Cement
Industrial rubber cement is typically used in commercial settings where stronger, more durable bonds are needed. Its drying time is longer due to its thicker application and stronger adhesive properties.
- Dries to the touch: 15-30 minutes
- Full curing: Up to 24 hours, depending on thickness and environmental conditions
Factors Affecting Drying Time
Several factors can influence how fast rubber cement dries:
- Application Thickness: Thicker layers take longer to dry.
- Environmental Conditions: Warm, dry conditions speed up drying times, while cool, humid conditions slow it down.
Drying Times Table
Type of Rubber Cement | Dries to the Touch | Full Bonding Strength | Full Curing |
---|---|---|---|
Quick-Drying Rubber Cement | 5-10 minutes | 30 minutes to 1 hour | – |
Standard Rubber Cement | 10-15 minutes | 1-2 hours | – |
Industrial Rubber Cement | 15-30 minutes | – | Up to 24 hours |
This table summarizes the drying times for each type, helping you choose the right one for your needs.
Tips for Optimal Drying
Achieving optimal drying time for rubber cement is crucial for a successful outcome in your projects. By following certain guidelines, you can ensure that the rubber cement dries quickly and effectively.
Apply in Thin Layers
Applying thin layers of rubber cement helps speed up the drying process. The solvent evaporates faster from a thin application, reducing the overall drying time.
- Even Spread: Use a brush or applicator to spread the rubber cement thinly and evenly.
- Layer Checks: Ensure that each layer is fully dry before applying additional coats.
- Avoid Puddles: Prevent pooling of adhesive, as thicker puddles take significantly longer to dry.
Ensure Proper Ventilation
Adequate ventilation accelerates the drying of rubber cement by promoting faster solvent evaporation.
- Open Spaces: Work in well-ventilated areas, preferably outdoors or in large rooms.
- Fans: Use fans to improve air circulation around the application area.
- Windows: Keep windows open to allow fresh air in and fumes out.
Maintain Ideal Temperature and Humidity
Temperature and humidity significantly affect the drying time of rubber cement. Ensuring the right conditions can optimize the drying process.
- Temperature Range: Maintain a temperature between 65°F and 85°F. Lower temperatures slow drying, while higher temperatures expedite it.
- Humidity Levels: Aim for low humidity levels (below 50%). High humidity prolongs drying as the air becomes saturated with moisture.
- Consistency: Keep environmental conditions consistent throughout the drying process to avoid extending drying times.
By adhering to these tips, you can ensure that your rubber cement application dries efficiently, providing strong and durable bonds for your projects.
Troubleshooting Common Issues
Problems with rubber cement drying may arise during your projects. Understanding these issues can lead to better outcomes and save time.
Extended Drying Time
Extended drying times can hinder project progress. Multiple factors cause this:
- Thickness of Application: Thick layers take longer to dry. Apply thin, even coats for faster drying.
- Environmental Conditions: Cold, humid environments lengthen drying times. Ensure a warm, dry workspace.
If drying takes too long, check these conditions first. Optimizing these factors can significantly reduce waiting times.
Incomplete Bonding
Incomplete bonding compromises the integrity of your project. Common causes include:
- Improper Application: Uneven layers or inadequate pressure during application lead to weak bonds.
- Dirty Surfaces: Dirt and grease can prevent proper adhesion. Clean surfaces thoroughly before application.
- Incorrect Cement Type: Using rubber cement meant for different materials can cause weak bonds. Select the appropriate type for your specific project.
Residual Adhesive
Residual adhesive can be an eyesore and affect the project’s finish. Causes for leftover adhesive include:
- Thick Layers: Applying too much cement can leave residues. Use thin layers to avoid excess.
- Improper Drying: Inadequate drying time can cause incomplete curing, leaving sticky residues. Allow sufficient drying time based on the environment.
Steps to Troubleshoot Common Issues
By following these steps, you can troubleshoot and resolve common issues with rubber cement drying and bonding effectively:
- Assess Environment: Ensure the workspace is warm and dry. Use heaters or dehumidifiers if necessary.
- Adjust Application: Apply thin, even layers. Use a brush or applicator for consistent coverage.
- Select Proper Cement: Choose a formulation designed for the specific materials of your project.
- Prepare Surfaces: Clean surfaces thoroughly to ensure strong adhesion. Use alcohol or a degreaser for best results.
- Allow Proper Drying Time: Wait for the recommended drying time based on the environmental conditions and type of rubber cement.
Factor | Optimal Condition |
---|---|
Temperature | 70-85°F (21-29°C) |
Humidity | Below 60% |
Air Circulation | Good ventilation, open windows |
Ensuring optimal conditions can drastically improve drying times and the bonding strength of your rubber cement applications.
These solutions can help you resolve common issues, ensuring strong and durable results. Adjusting application techniques and maintaining an optimal environment are key to successful rubber cement use.
Conclusion
Mastering the drying times of rubber cement is essential for the success of your projects. By considering factors like temperature, humidity, and application thickness, you can better plan and execute your work. Remember to choose the right type of rubber cement for your specific needs and follow best practices for application and drying. This knowledge will help you achieve strong and durable bonds, ensuring your crafts and repairs are done efficiently and effectively.
Frequently Asked Questions
What factors affect the drying time of rubber cement?
Temperature, humidity, and the thickness of the rubber cement application largely influence drying time. Warmer temperatures and dry conditions speed up the process, while cold and humid conditions slow it down. Thin layers dry faster than thick ones.
How long does quick-drying rubber cement take to dry?
Quick-drying rubber cement becomes touch-dry in 5-10 minutes and reaches full bonding strength within 30 minutes to 1 hour.
What is the drying time for standard rubber cement?
Standard rubber cement takes about 10-15 minutes to dry to the touch and approximately 1-2 hours for optimal adhesion.
How long does industrial rubber cement take to fully cure?
Industrial rubber cement dries to the touch in 15-30 minutes but can take up to 24 hours to fully cure.
How can I speed up the drying time of rubber cement?
Apply rubber cement in thin layers, ensure proper ventilation, and maintain an ideal temperature and humidity to enhance drying efficiency.
Why is it important to let rubber cement dry before applying a patch?
Allowing rubber cement to dry ensures solvents evaporate, preventing trapped gases that could compromise the repair’s integrity.
How long should I let rubber cement dry on a tire plug?
It is recommended to let rubber cement dry for ten minutes before inflating the tire to ensure proper adhesion of the plug to the tire.