What Will JB Weld Not Stick To: Key Surfaces Explained
When you’re tackling a repair project, JB Weld often comes to mind as a go-to adhesive for its renowned strength and versatility. But, even this miracle worker has its limitations. Knowing what JB Weld won’t stick to can save you time and frustration, ensuring your repairs hold up under pressure.
Understanding the surfaces that JB Weld can’t adhere to helps you choose the right materials and methods for your project. Whether you’re fixing a broken tool or patching up a leaky pipe, being aware of these limitations ensures your repairs are both effective and durable. Let’s jump into what JB Weld won’t stick to so you can plan your next project with confidence.
Key Takeaways
- JB Weld is an epoxy-based adhesive known for its strong bonding properties, but it does not adhere well to certain materials.
- Surfaces such as flexible rubber, canvas, polypropylene, and polyethylene generally resist JB Weld bonding due to their specific properties.
- Greased or coated surfaces can interfere with JB Weld’s curing process, making it essential to clean and prepare surfaces properly.
- Knowing JB Weld’s limitations ensures you choose the right adhesive for effective and durable repairs.
- Using release agents like vegetable oil and petroleum jelly or physical barriers like shrink wrap and painter’s tape can prevent JB Weld from sticking to unwanted areas.
- Proper surface preparation, including cleaning, abrading, and drying, is crucial for optimizing JB Weld’s adhesion.
What Is JB Weld?
JB Weld is an epoxy-based adhesive known for its exceptional bonding capabilities. It’s a popular choice for various repair projects due to its versatility and strength. Here’s a detailed breakdown of what JB Weld offers and its applications:
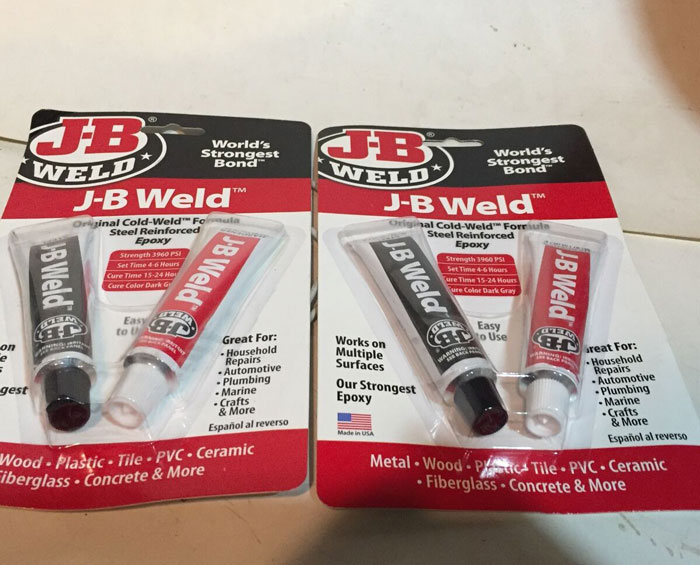
Key Features of JB Weld
- Epoxy-Based: JB Weld consists of two primary components—a resin and a hardener. When mixed, they create a robust adhesive.
- Strong Bonding: Renowned for its strong bonding properties, JB Weld is effective for repairing metal, plastic, wood, and many other materials.
- Versatility: It’s suitable for multiple applications, ranging from household repairs to automotive fixes.
Common Applications
- Metal Repairs: Ideal for fixing metal components in vehicles, machinery, and household items.
- Plastic Repairs: Effective for hard plastic items like toys and tools.
- Wood Repairs: Handy for fixing broken wooden furniture and household structures.
Important Considerations
When using JB Weld, some surfaces do not achieve optimal adhesion. Here’s a list of surfaces where JB Weld generally performs poorly:
- Flexible Rubber Surfaces: The flexibility of rubber makes it difficult for JB Weld to establish a firm bond.
- Canvas: The porous nature of canvas prevents reliable adhesion.
- Polypropylene and Polyethylene: These plastics tend to resist bonding with JB Weld.
- Greased or Coated Surfaces: Oil, grease, or other coatings can interfere with the curing process.
Adhesion Chart
Below is a table summarizing JB Weld’s adhesion results on various surfaces:
Material Type | Adhesion Quality |
---|---|
Metal | Excellent |
Hard Plastic (e.g., ABS) | Good |
Wood | Good |
Flexible Rubber | Poor |
Canvas | Poor |
Polypropylene and Polyethylene | Poor |
Greased/Coated Surfaces | Poor |
- Surface Preparation: Clean the surfaces to remove dirt, oil, and grease. A roughened surface improves adhesion.
- Mixing Ratio: Combine equal parts of the resin and hardener.
- Application: Apply the mixture to the prepared surface and allow it to cure as per the manufacturer’s instructions.
Knowing the materials JB Weld adheres to and those it does not bond well with will help in planning effective repair projects. This ensures reliable, durable fixes and better project outcomes.
What Will JB Weld Not Stick To?
Understanding the surfaces that JB Weld cannot adhere to is crucial for successful repairs. Knowing these limitations helps in selecting the right adhesive for each project and ensures durable and effective results.
Understanding Material Compatibility
JB Weld is an epoxy-based adhesive known for its strong bonding properties. But, not all materials are suitable for epoxy adhesion. Some surfaces don’t form strong bonds with JB Weld due to their specific characteristics.
Key Points:
- Surface Properties: Surfaces with too much flexibility or those that are greasy can affect adhesion.
- Material Types: Certain plastics and rubbers resist epoxy bonding.
Common Surfaces It Won’t Bond To
Even though JB Weld is versatile, it has notable exceptions. Here are the common surfaces where JB Weld fails to bond effectively:
- Flexible Rubber Surfaces: Rubber surfaces that are too flexible do not offer a stable area for JB Weld to adhere.
- Canvas: The texture and absorbency of canvas make it difficult for JB Weld to form a strong bond.
- Flexible Plastics: Plastics like polypropylene and polyethylene do not bond well with JB Weld due to their chemical composition and flexibility.
Unique Situations and Exceptions
Several specific conditions can hinder JB Weld’s adhesion capabilities, even on materials it typically bonds to:
- Grease and Coatings: Surfaces coated with grease or certain substances inhibit the curing process of JB Weld. Always ensure surfaces are clean and free of such coatings.
- Improperly Prepared Surfaces: If the surface isn’t clean or properly prepared, JB Weld will not adhere well.
- Certain Plastics: Apart from flexible plastics, other types of plastics with low surface energy might also resist bonding.
Material Type | Reason for Non-Adherence |
---|---|
Flexible Rubber | Too flexible to provide a stable bond |
Canvas | Textured and absorbent nature |
Polypropylene | Chemical composition resists bonding |
Polyethylene | Flexible and chemically resistant |
Grease-coated surfaces | Interferes with curing process |
Understanding these limitations ensures you choose the right adhesive for every repair project. Proper surface preparation and material compatibility are crucial for achieving a strong and durable bond with JB Weld.
How To Prevent JB Weld From Sticking
Sometimes, when using JB Weld, you might need to prevent it from sticking to certain surfaces. Knowing how to achieve this can make your projects more versatile and manageable. Here are effective methods to keep JB Weld from adhering when it’s necessary.
Use of Release Agents
Applying a release agent creates a barrier that prevents JB Weld from bonding to surfaces.
Release Agent Examples:
- Vegetable Oil: Applying a thin layer of vegetable oil to the surface can effectively prevent JB Weld from sticking. This method is particularly useful when molding or shaping.
- Petroleum Jelly: A light coating of petroleum jelly can also serve as an excellent release agent, ensuring the epoxy doesn’t adhere.
To use a release agent:
- Clean the surface to remove any debris.
- Apply a thin, even layer of the release agent.
- Proceed with your JB Weld application.
Implementing Barriers
Physical barriers ensure JB Weld doesn’t contact the surface you want to protect.
- Shrink Wrap: Coating the surface with shrink wrap acts as a protective layer that the epoxy can’t penetrate.
- Painter’s Tape: Applying painter’s tape to the areas you want to keep clean can provide a temporary barrier.
Steps to use barriers:
- Clean and dry the surface.
- Cover the area with shrink wrap or painter’s tape.
- Apply JB Weld as needed.
Utilizing these methods will help you manage your JB Weld projects with greater precision. Use release agents or barriers depending on your specific needs to prevent the epoxy from sticking where it’s not wanted.
Factors Affecting JB Weld Adhesion
Various factors influence the effectiveness of JB Weld’s bonding abilities. Awareness of these factors ensures strong and durable repairs.
Surface Preparation
Surface preparation critically impacts JB Weld adhesion.
- Cleaning: Use a degreaser or solvent to clean surfaces. Remove dirt, grease, oil, paint, rust, and debris.
- Abrading: Lightly sand the area to create a rough texture, enhancing the epoxy’s grip.
- Drying: Ensure the surface is dry. Moisture can interfere with adhesion.
Environmental Conditions
Environmental factors also affect how JB Weld bonds to surfaces.
- Temperature: Apply JB Weld in temperatures between 50°F (10°C) and 90°F (32°C). Extreme temperatures weaken the bond.
- Humidity: High humidity can slow the curing process. Maintain a controlled environment for optimal results.
- Ventilation: Ensure good ventilation to dissipate fumes and help the epoxy cure properly.
Conclusion
Understanding JB Weld’s limitations is crucial for successful repairs. Knowing which surfaces it won’t adhere to, like flexible rubber and certain plastics, helps you avoid failed projects. Proper surface preparation, including cleaning and sanding, ensures the best bond. Also using release agents and physical barriers can help manage where JB Weld sticks enhancing your control over the repair process.
By following these guidelines and considering environmental factors like temperature and humidity you’ll maximize JB Weld’s effectiveness. This knowledge empowers you to tackle repairs with confidence ensuring durable and reliable results every time.
Frequently Asked Questions
What is JB Weld used for?
JB Weld is an epoxy-based adhesive known for its strong bonding properties, suitable for various repairs including metal, plastic, and wood.
Can JB Weld bond to all types of plastics?
No, JB Weld does not bond well to certain plastics like polypropylene and polyethylene due to their specific properties.
How should I prepare a surface before using JB Weld?
Clean the surface with a degreaser or solvent, lightly sand to create a rough texture, and ensure the area is dry for optimal adhesion.
What can I use to prevent JB Weld from sticking to certain areas?
You can use release agents like vegetable oil or petroleum jelly and physical barriers such as shrink wrap or painter’s tape to prevent bonding in unwanted areas.
Does JB Weld work on flexible materials?
No, JB Weld is not suitable for flexible materials like rubber or canvas as it requires a rigid surface for effective bonding.
How strong is JB Weld once it cures?
JB Weld has a tensile strength of 5020 PSI and can handle significant stress once fully cured.
What are the ideal environmental conditions for using JB Weld?
Maintain a temperature between 50°F and 90°F, control humidity, and ensure good ventilation for the best results.
What are some common surfaces JB Weld fails to adhere to?
JB Weld often fails to adhere to surfaces like flexible rubber, canvas, and certain plastics such as polypropylene and polyethylene.
How can I make sure JB Weld adheres properly?
Ensure proper surface preparation, maintain suitable environmental conditions, and follow the correct mixing ratio of JB Weld components.
Is JB Weld a permanent solution for repairs?
While JB Weld provides a strong and durable bond, its effectiveness depends on proper application and surface compatibility, making it a potentially permanent solution for many repairs.