JB Weld vs Epoxy: Which Adhesive is Best for Your Needs?
When it comes to fixing broken items or crafting durable projects, choosing the right adhesive is crucial. You’ve probably heard of JB Weld and epoxy, two popular options known for their strong bonding capabilities. But which one should you use for your specific needs?
Key Takeaways
- Adhesive Strength and Durability: JB Weld offers superior strength and durability due to its metallic fillers and is ideal for metal repairs and high-stress applications. Epoxy provides versatile bonding capabilities with strength varying by formulation.
- Curing Time: JB Weld typically takes 4-6 hours to set and 12-24 hours to reach full strength, while epoxy has a faster setting time, making it more suitable for quick repairs.
- Temperature Resistance: JB Weld excels in high-temperature environments, making it suitable for engine repairs and other heat-exposed applications. Epoxy’s temperature resistance varies but is generally lower than JB Weld.
- Versatility and Applications: Epoxy is highly versatile, suitable for bonding different materials like wood, plastic, and ceramics. JB Weld is primarily used for metal repairs and applications requiring enhanced strength and heat resistance.
- User Preferences and Reviews: Users prefer JB Weld for heavy-duty, high-temperature repairs, while epoxy is favored for its ease of use, versatility, and quick-setting properties. Both adhesives receive positive reviews for their specific strengths.
Understanding JB Weld and Epoxy
Choosing the right adhesive for your repair or construction project can make a significant difference in the durability and longevity of the bond. This section provides detailed insights into JB Weld and epoxy, two popular adhesive options known for their strong bonding capabilities.
What Is JB Weld?
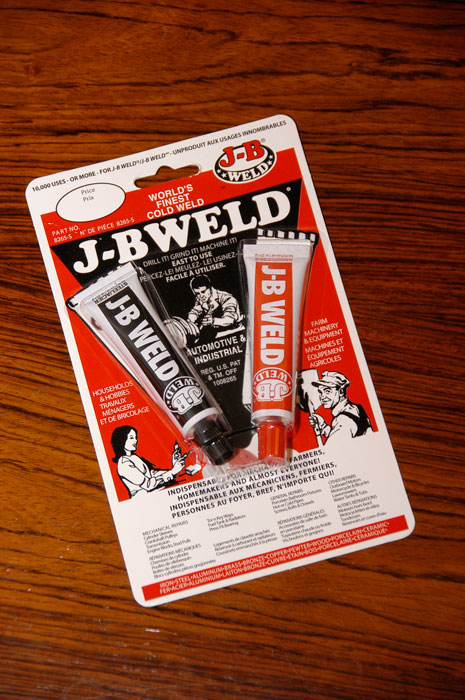
JB Weld is a two-part epoxy adhesive renowned for its robustness and versatility. Let’s break down its key aspects:
Composition:
- Metal Dust: Enhances strength and hardness, similar to concrete with gravel
- Epoxy Resin: Provides chemical resistance and strong adhesion
Properties:
- High Strength: Can be drilled and tapped once cured
- Temperature Resistance: Effective in high-temperature applications
- Hardness: Substantially harder than regular epoxy when cured
Applications:
- Metal Repairs: Ideal for engine components and other metal parts
- Mechanical Stress: Withstands high mechanical stress
Strength:
- Original Formulation: Stronger than some newer versions and other epoxy types
What Is Epoxy?
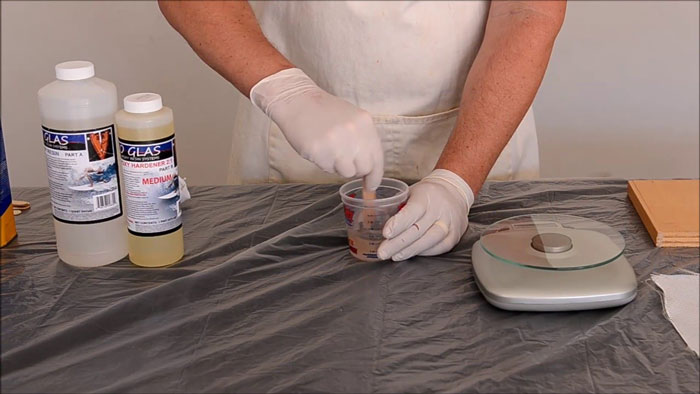
Epoxy, a versatile adhesive, is commonly used in both industrial and DIY applications. Here are its fundamental characteristics:
Composition:
- Resin: Provides rigidity and structural integrity
- Hardener: Cures the resin, forming a solid bond
Properties:
- Versatility: Bonds various materials including wood, plastic, and metal
- Chemical Resistance: Resists various chemicals once cured
- Curing Time: Generally faster than JB Weld
Applications:
- Construction: Used in flooring, countertops, and coating applications
- Repair Work: Ideal for general-purpose repairs due to its versatility
Strength:
- Varies by Formulation: Strength and properties can differ based on specific epoxy formulations
Property | JB Weld | Regular Epoxy |
---|---|---|
Composition | Metal Dust, Epoxy Resin | Resin, Hardener |
Hardness | Substantially harder when cured | Depends on formulation |
Temperature Resistance | High (suitable for engine repairs) | Ranges depending on formulation |
Curing Time | Longer | Usually faster |
Versatility | Primarily for metal, especially high-stress areas | Bonds wood, plastic, metal, and more |
Drillable | Yes (can be drilled and tapped) | Varies; usually not as hard as JB Weld |
Understanding these key properties helps you make an well-informed choice. Whether repairing metal engine parts or crafting versatile adhesive bonds, knowing the specifics of JB Weld and epoxy ensures the best outcome for your projects.
Key Differences Between JB Weld and Epoxy
When it comes to choosing between JB Weld and epoxy for your projects, understanding their key differences is crucial. This section breaks down the composition, properties, strength, durability, and application methods of each adhesive to help you make a well-well-informed choice.
Composition and Properties
JB Weld:
- Components: Resin, hardener, metallic filler (often powdered steel).
- Characteristics: Enhanced strength, heat resistance; suitable for sanding and shaping after hardening.
Epoxy:
- Components: Resin, hardener without metallic fillers.
- Characteristics: More flexible in application but less robust in certain mechanical properties compared to JB Weld.
Strength and Durability
JB Weld:
- Strength: Superior due to metallic fillers.
- Durability: High resistance to heat and mechanical stress; ideal for metal repairs.
Epoxy:
- Strength: Generally strong but lacks the added strength of JB Weld.
- Durability: Can be brittle and may not hold as well under high stress or heat.
Application Methods
JB Weld:
- Usage: Ideal for applications requiring high strength and heat resistance.
- Preparation: Mix resin and hardener, apply to the surface, and shape as needed.
- Example: Repairing cracked engine blocks.
Epoxy:
- Usage: Versatile for various industrial and DIY projects.
- Preparation: Mix resin and hardener, apply to the surface.
- Example: Bonding wood, metal, ceramics.
Property | JB Weld | Epoxy |
---|---|---|
Composition | Resin, hardener, metallic filler | Resin, hardener |
Strength | Superior due to metallic filler | Generally strong but less robust |
Durability | High resistance to heat and mechanical stress | Can be brittle under stress/heat |
Application Method | Mix, apply, shape | Mix, apply |
Ideal Use Case | Metal repairs | General repairs, bonding various materials |
Choosing the right adhesive depends on your specific project needs. Use JB Weld for tasks requiring exceptional strength and heat resistance. Opt for epoxy when flexibility in application and versatility are important.
Use Cases and Suitability
Choosing between JB Weld and epoxy depends largely on the specific requirements of your project. Each adhesive has unique properties making them more suitable for certain applications.
Best Uses for JB Weld
High Temperature Applications:
JB Weld stands out in high-temperature environments. It retains strength and integrity better than many other epoxies under heat, making it ideal for engine parts, valve seats, and other mechanical components subjected to intense heat.
Metal Bonding:
JB Weld excels in bonding metal surfaces. Containing metal dust, it offers enhanced strength and tenacity. Use JB Weld for repairs on engine parts and other metal-based items.
Durability and Hardness:
Once cured, JB Weld forms a hard, durable bond that can be drilled and tapped. This makes it suitable for applications requiring the bonded material to withstand significant stress and wear.
Best Uses for Epoxy
Versatile Applications:
Epoxy is highly versatile, making it ideal for a wide range of applications from DIY projects to industrial repairs. Its compatibility with numerous materials such as wood, plastic, and ceramics is a key advantage.
Chemical Resistance:
Epoxy offers excellent resistance to chemicals, making it suitable for applications involving exposure to solvents, acids, and other harsh substances. This property is particularly valuable in industrial settings.
Flexible Bonding:
Unlike JB Weld, epoxy provides a more flexible bond. This characteristic is beneficial for projects requiring a less rigid adhesive, such as bonding delicate materials or surfaces subject to minor movements or vibrations.
Property | JB Weld | Epoxy |
---|---|---|
Temperature Resistance | High | Moderate |
Best for Bonding | Metal | Multiple Materials |
Durability and Hardness | Excellent, can be drilled | Good, but more flexible |
Chemical Resistance | Moderate | High |
Curing Time | Longer | Varies, generally faster |
Understanding the strengths and limitations of JB Weld and epoxy helps you choose the right adhesive for your specific project. For high-temperature and metal bonding jobs, JB Weld is the better option. Epoxy, on the other hand, offers versatility and chemical resistance, making it ideal for a broad range of applications.
Performance Comparison
When choosing between JB Weld and epoxy, it’s essential to understand how each performs under various conditions. This section breaks down their setting times, curing processes, shear strength, adhesion properties, and resistance to environmental factors.
Setting Time and Curing Process
JB Weld
JB Weld is a two-part epoxy that you must mix before application. It typically takes 4-6 hours to set and 12-24 hours to reach full strength, making it ideal for tasks where a strong, durable bond is necessary and there is ample time for curing.
Epoxy
Epoxy’s setting times can vary widely:
- 5-minute epoxies: Set quickly but may take longer to reach full strength.
- Longer-setting epoxies: May require additional curing methods like baking to achieve their full properties.
Here’s a quick comparison:
Product | Set Time | Full Strength Time |
---|---|---|
JB Weld | 4-6 hours | 12-24 hours |
5-Minute Epoxy | 5 minutes | Varies (up to 24 hours) |
Standard Epoxy | 30 minutes to 1 hour | 24-48 hours |
Shear Strength and Adhesion
JB Weld
Known for high shear strength due to metallic fillers, JB Weld excels in metal repairs. It outperforms other adhesives in shear strength tests, especially on metal surfaces, making it a preferred choice for metal bonding tasks.
Test Results
In comparative tests:
- JB Weld Original: Demonstrated superior shear strength over newer JB Weld versions and other epoxies like Gorilla epoxy and Loctite.
Resistance to Environmental Factors
JB Weld
JB Weld shows high resistance to heat and mechanical stress, making it suitable for applications subjected to extreme conditions like engine parts and metal repairs.
Epoxy
Epoxies offer varying levels of resistance depending on their formulation:
- Standard Epoxies: Generally provide good chemical and temperature resistance but may not match the high heat resistance of JB Weld.
- Specialized Epoxies: Can be tailored to withstand specific environmental factors like UV light or harsh chemicals.
Here’s a summary table:
Adhesive | Heat Resistance | Chemical Resistance | UV Resistance |
---|---|---|---|
JB Weld | Excellent | Good | Moderate |
Standard Epoxy | Good | Good | Varies |
Specialized Epoxy | Varies | Excellent | Good to Excellent |
Understanding the performance characteristics of JB Weld and epoxy helps you choose the best adhesive for your specific needs, ensuring strong and durable bonds in your projects.
User Experiences and Reviews
When deciding between JB Weld and epoxy, user experiences and reviews offer valuable insights. Both products have loyal followings, but users often highlight differing strengths based on their specific needs.
JB Weld
JB Weld is often praised for its exceptional bond strength, especially on metal surfaces. It’s commonly chosen for automotive repairs, heavy-duty construction, and high-stress applications.
- Bond Strengths: Users frequently comment on JB Weld’s ability to withstand significant mechanical stress.
- Heat Resistance: Many users report successful outcomes in high-temperature environments, such as engine repairs.
- Durability: Reviews often note the long-lasting nature of JB Weld, emphasizing its robustness over time.
Example: One user mentioned using JB Weld to repair a cracked engine block. Even though extreme temperatures, the bond held firm for years.
Epoxy
Epoxy receives high marks for its versatility and ease of use. It’s a go-to choice for various DIY projects, including crafts, household repairs, and light construction.
- Versatility: Users appreciate epoxy’s ability to bond diverse materials like wood, plastic, and ceramics.
- Curing Time: Reviews vary, with many noting the availability of quick-setting and slow-curing options.
- Chemical Resistance: Epoxy is well-regarded for resisting chemicals, making it suitable for environments where chemical exposure is frequent.
Example: A reviewer used epoxy to create a custom countertop. The finished product was praised for its aesthetic appeal and durability against spills and stains.
Comparative Data
Here’s a detailed comparison based on user reviews and performance metrics:
Feature | JB Weld | Epoxy |
---|---|---|
Typical Setting Time | 4-6 hours | Varies (5 minutes to several hours) |
Full Cure Time | 12-24 hours | Varies (12-24 hours to several days) |
Shear Strength | High (particularly on metals) | Moderate to high (depending on type) |
Heat Resistance | Excellent (up to 550°F) | Varies (generally less than JB Weld) |
Chemical Resistance | Good | Excellent (depending on formulation) |
Ease of Use | Moderate (requires careful mixing) | High (pre-mixed options available) |
Summary
When choosing between JB Weld and epoxy, consider these user experiences and performance metrics. JB Weld stands out for heavy-duty, high-stress, and metal-focused applications, while epoxy offers versatility and ease for a wide range of materials and projects. Reviews suggest aligning your choice with the specific demands of your project for best results.
Conclusion
Choosing between JB Weld and epoxy depends on your project’s specific needs. If you’re dealing with high-stress, high-temperature applications, JB Weld’s superior strength and heat resistance make it the ideal choice. It’s particularly effective for metal repairs and mechanical components.
On the other hand, if versatility and ease of use are your priorities, epoxy offers a flexible solution suitable for a wide range of materials and applications. Its varying setting times and chemical resistance make it a go-to for many DIY projects.
By understanding the unique properties of each adhesive, you can make an well-informed choice that ensures the success and durability of your repairs or creations.
Frequently Asked Questions
Which epoxy is the strongest?
The strongest epoxy glue you can purchase is likely Systemthree’s T-88. This two-part adhesive has a tensile strength of 7000 psi, well above the average strength for epoxies. It offers outstanding adhesion and durability on various materials and is designed to resist adverse conditions.
Is J-B Weld waterproof?
Yes, J-B Weld is water-resistant, petroleum/chemical-resistant (when hardened), and acid-resistant. It can also withstand shock, vibration, and extreme temperature fluctuations. J-B Weld can handle a constant temperature of 500 °F (260 °C) and up to 600 °F (316 °C) for short durations.
Does J-B Weld stick to concrete?
J-B Weld Original can be used to repair many different materials, including metal, wood, plastic, ceramic, fiberglass, brick, and concrete. It’s a versatile adhesive suitable for a wide range of applications.
How many pounds of force can J-B Weld hold?
When mixed at a ratio of 1:1, J-B Weld forms a permanent bond that can withstand a tensile strength of 5020 PSI. It can be shaped, tapped, filed, sanded, and drilled after curing, achieving a durable hard bond overnight.
How strong is J-B Weld after 4 hours?
After four hours, J-B Weld will be strong enough for light use but won’t reach its maximum strength for another 24 hours. For repairs under heavy stress, it’s best to wait 24 hours before putting it to use.
What makes J-B Weld different from regular epoxy?
J-B Weld includes metal dust, offering superior strength and high resistance to heat and mechanical stress, making it ideal for metal repairs. In contrast, regular epoxy is more versatile but generally lacks the added strength of J-B Weld, suitable for various industrial and DIY projects.
Can epoxy be used for high-temperature applications?
Standard epoxy can withstand moderate temperatures but J-B Weld is specifically formulated for high-temperature conditions, offering better performance in such scenarios. Always check the specifications to ensure the epoxy suits your project’s thermal requirements.
How long does it take for epoxy to cure?
Epoxy setting times vary widely, from quick-setting 5-minute options to longer-setting varieties that may require several hours or additional curing methods. It’s essential to consult the product’s instructions for precise curing times.
What’s the difference in the application methods between J-B Weld and epoxy?
J-B Weld typically requires mixing metallic fillers with epoxy resin, making it ideal for high-stress repairs like engine parts. Regular epoxy generally comes as a two-part resin and hardener, offering more flexibly in diverse applications.
Which adhesive should I choose for general repairs?
For high-strength and high-temperature applications, J-B Weld is recommended. For projects requiring versatility and chemical resistance, regular epoxy is a better option. Choose based on the specific demands of your repair or construction task.