Loctite 638 vs 680: Which Adhesive is Right for Your Project?
When you’re working on securing cylindrical parts, choosing the right adhesive can make all the difference. Loctite 638 and 680 are two popular options, but how do you decide which one fits your needs best? Both are high-strength retaining compounds, yet they offer unique features that cater to different applications.
In this text, you’ll discover the key differences between Loctite 638 and 680, from their bonding capabilities to their optimal use cases. By understanding these distinctions, you can make an well-informed choice, ensuring your projects are not only durable but also efficient. Let’s jump into the specifics of these powerful adhesives.
Key Takeaways
- Application Suitability: Loctite 638 is ideal for small gaps up to 0.010 inches and precision applications like securing shafts and gears, while Loctite 680 is better for larger gaps up to 0.015 inches and versatile conditions.
- Curing Time: Loctite 638 cures rapidly within 5 minutes, making it suitable for quick assembly projects. Loctite 680 cures in about 10 minutes at room temperature, providing flexibility in various environmental conditions.
- Viscosity and Tolerance: Loctite 638 has high viscosity suitable for thicker gap fills, whereas Loctite 680’s low viscosity is excellent for tight fits and relaxed machining tolerances.
- Strength and Durability: Both adhesives offer high strength; Loctite 680 provides a specified shear strength of 4,000 psi, making it robust for high-stress applications.
- Environmental Resistance: Loctite 638 has high oil tolerance and corrosion resistance, suitable for high-load applications, including those with incidental food contact. Loctite 680 offers excellent performance with active and passive metals and does not require primers for curing.
Overview Of Retaining Compounds
Understanding the unique characteristics of Loctite 638 and Loctite 680 is crucial for choosing the right retaining compound for your project. Both products offer high strength and excellent performance, but they cater to different applications and requirements.
Key Characteristics and Applications
Loctite 638:
- Gap Filling: Designed for narrow bond gaps, typically up to 0.010 inches (0.25 mm) radial clearance. This compound works best for small clearances where precision is essential.
- Curing: Cures in the absence of air between close-fitting metal surfaces, making it suitable for both active and passive metals. The absence of oxygen ensures rapid curing and a strong bond.
- Properties: High strength, high temperature resistance, and good oil tolerance. These attributes make it ideal for securing shafts, gears, pulleys, and similar cylindrical parts where durability is critical.
- Fixture Time: Fixes parts in as little as 5 minutes, allowing quick assembly and reduced downtime.
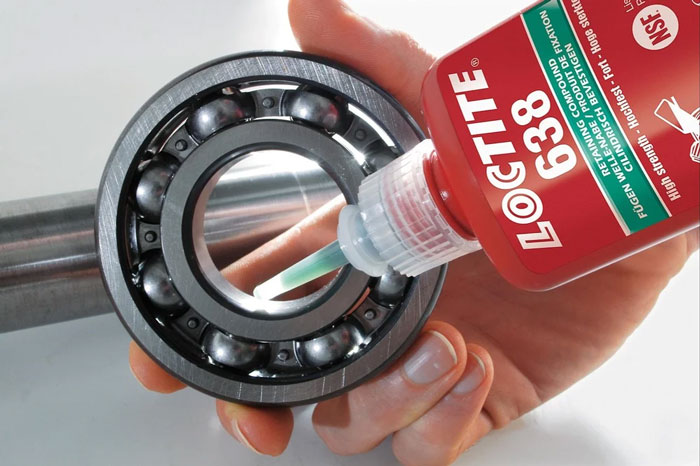
Loctite 680:
- Gap Filling: Suitable for parts with clearances up to 0.015 inches (0.38 mm) diametral clearance. This compound accommodates larger tolerances.
- Curing: High viscosity, room temperature curing adhesive. Fixes in 10 minutes, providing flexibility for various environmental conditions.
- Properties: High strength, allows relaxed machining tolerances, and replaces mechanical fasteners like clamp rings, set screws, and snap rings. Delivers a shear strength of 4,000 psi, ensuring robust joint integrity.
Comparison Table
Feature | Loctite 638 | Loctite 680 |
---|---|---|
Gap Filling | Up to 0.010 inches (0.25 mm) radial | Up to 0.015 inches (0.38 mm) diametral |
Curing Time | 5 minutes | 10 minutes |
Curing Conditions | Absence of air between metal surfaces | Room temperature |
Viscosity | Low | High |
Temperature Resistance | High | High |
Applications | Shafts, gears, pulleys, cylindrical parts | Parts with larger clearances, replaces clamp rings, set screws, snap rings |
Shear Strength | Not specified | 4,000 psi |
Summary
Selecting between Loctite 638 and 680 depends on your specific application requirements. If dealing with tight tolerances and requiring quick fixture times, Loctite 638 is ideal. For applications that need flexibility in machining tolerances and high strength, Loctite 680 is the better choice. By understanding these differences, you can ensure optimal performance and longevity for your mechanical assemblies.
Features And Benefits
Selecting the right adhesive is crucial for mechanical assemblies, where securing cylindrical parts is essential. Two popular retaining compounds, LOCTITE 638 and LOCTITE 680, offer unique features that cater to different applications. Here’s a detailed comparison to help you make an well-informed choice.
Load Distribution
LOCTITE 638:
- High Strength: This adhesive is ideal for high-load bearing applications. It efficiently distributes dynamic, axial, and radial loads, ensuring strong, durable bonds.
- Thick Viscosity: With its high viscosity, LOCTITE 638 fills larger gaps up to 0.25 mm (0.010 in), making it suitable for slip fit parts that may have more significant tolerances.
LOCTITE 680:
- High Strength: Similar to LOCTITE 638, LOCTITE 680 provides robust load distribution, ensuring your parts remain secure under substantial stress.
- Low Viscosity: LOCTITE 680’s low viscosity is perfect for smaller gaps and tight fits, making it suitable for precise applications where excess adhesive might be problematic.
Corrosion Prevention
LOCTITE 638:
- Oil Tolerant: The ability to bond through contaminants, including oils and corrosion protection fluids, enhances its performance in various industrial environments.
- NSF P1-Certified: This certification for incidental food contact applications ensures that LOCTITE 638 can be used in industries that require stringent hygiene standards.
LOCTITE 680:
- Active and Passive Metals: LOCTITE 680 cures anaerobically, meaning it works well in the absence of air. This feature makes it suitable for both active and passive metals, providing excellent corrosion resistance.
- Primerless Cure: Rapid curing without the need for additional primers makes LOCTITE 680 efficient and easy to use, ensuring a secure bond even in slightly contaminated conditions.
Stress Reduction
LOCTITE 638:
- Primerless Cure: Similar to LOCTITE 680, it cures rapidly without activators for most applications. This feature speeds up assembly processes and reduces internal stresses caused by long curing times.
- Resilient Bonding: Capable of withstanding dynamic loads, LOCTITE 638 helps manage stresses induced during operation, minimizing the risk of part failure.
LOCTITE 680:
- Anaerobic Cure: Curing in the absence of air ensures a more uniform bond, reducing internal stresses and enhancing the overall integrity of the assembled parts.
- Adaptable Performance: Fault-tolerant in its curing process allows LOCTITE 680 to perform effectively even under less-than-ideal conditions, minimizing stress concentrations.
Feature | LOCTITE 638 | LOCTITE 680 |
---|---|---|
Viscosity | High – up to 0.25 mm (0.010 in) gap | Low – ideal for tight fits |
Cure Type | Primerless | Primerless, Anaerobic |
Load Distribution | Dynamic, axial, radial | Substantial stress |
Oil Tolerance | Yes | Slightly oiled and contaminated |
Certifications | NSF P1-Certified | None |
Applications | Dynamic loads, slip fits | Precise fits, various environments |
Choosing between LOCTITE 638 and LOCTITE 680 depends on your specific application needs. For larger gaps and where contamination by oils is an issue, LOCTITE 638 stands out. For tighter fits and environments requiring high performance under varying conditions, LOCTITE 680 is the preferred choice.
Comparison: Loctite 638 Vs 680
Choosing the right adhesive is crucial for securing cylindrical parts in mechanical assemblies. Let’s compare Loctite 638 and Loctite 680 in terms of their mechanical properties, application scenarios, and performance in different environments.
Mechanical Properties
- Shear Strength
- Loctite 638: Known for its high strength, it is suitable for dynamic, axial, and radial loads, offering robust bonding.
- Loctite 680: Provides a high shear strength of 4,000 psi, making it ideal for high-strength applications.
- Gap Filling
- Loctite 638: Designed for slip fit parts with gaps up to 0.010 inches (0.25 mm), it efficiently fills smaller gaps, ensuring optimal performance on various metals.
- Loctite 680: Can fill diametral gaps up to 0.015 inches (0.38 mm), working well for slightly larger gaps compared to Loctite 638.
- Temperature Resistance
- Loctite 638: Offers good temperature resistance across various environmental conditions. Although the specific maximum temperature isn’t detailed, it performs reliably.
- Loctite 680: Not explicitly stated but generally provides excellent performance across a range of temperatures.
Application Scenarios
- Loctite 638
- Precision Applications: Ideal for securing shafts and gears.
- Quick Fixture Time: Cures in about 5 minutes, facilitating rapid project progression.
- High-Load Environments: Its NSF P1 certification makes it suitable for heavy-duty applications even in the presence of oil contaminants.
- Examples: Used in assembling high-load bearings and securing large industrial gears.
- Loctite 680
- Flexible Tolerance: Suitable for applications needing slightly larger gap fillings.
- Room Temperature Cure: No special temperature conditions are required for curing, making it versatile.
- Various Metals: Works well with both active and passive metals, ensuring good corrosion resistance.
- Examples: Suitable for parts requiring flexibility such as mechanical fasteners and cylindrical bondings in diverse environments.
Performance In Different Environments
- Loctite 638
- Oil Tolerance: High oil tolerance ensures effectiveness even when parts have slight lubrication residues.
- Corrosion Resistance: Prevents rust and corrosion under challenging conditions.
- High-Load Performance: Maintains bond integrity under heavy stress.
- Loctite 680
- Primerless Cure: Anaerobic cure that doesn’t require primers, enhancing usability in various conditions.
- Corrosion Resistance: Protects against corrosion for both active and passive metals.
- Versatile Conditions: Performs well across a wide range of environmental conditions.
Feature | Loctite 638 | Loctite 680 |
---|---|---|
Shear Strength | High (exact value unspecified) | 4,000 psi |
Gap Filling | Up to 0.010 in (0.25 mm) | Up to 0.015 in (0.38 mm) |
Temperature Range | Good (exact range unspecified) | Excellent (general performance) |
Cure Time | About 5 minutes | Room temperature cure |
Oil Tolerance | High | Medium |
Application | High-load, precise fits | Flexible tolerance, versatile applications |
Certification | NSF P1 | Not specified |
Selecting the appropriate Loctite adhesive depends on your specific requirements. Considerations like gap size, load stress, and environmental conditions will guide you toward the best choice for optimal performance in your mechanical assemblies.
Practical Applications
Choosing the right adhesive for securing cylindrical parts is crucial for mechanical assemblies. Both Loctite 638 and Loctite 680 offer unique advantages depending on the application requirements.
Small Gaps
Loctite 638: Ideal for small gaps up to 0.010 in (0.25 mm). It’s perfect for precision applications like securing shafts and gears due to its high strength and fast curing time.
- High Strength: Designed for high dynamic force or cyclic loading.
- Gap Fill: Effective on active and passive metal substrates, such as stainless steel.
- Temperature Resistance: Suitable for high-temperature environments and provides good oil tolerance.
Key Features:
- Dynamic Load Handling
- Quick Fixture Time:
- Effective on Multiple Metals
Medium Gaps
Loctite 680: Accommodates larger tolerances up to 0.015 in (0.38 mm), making it versatile for various fits and conditions.
- High Strength: Comparable to Loctite 638 but with relaxed machining tolerances.
- Room Temperature Curing: Cures effectively without the need for additional heating.
- High Viscosity: Ensures a strong bond even with larger gap sizes.
Key Features:
- Suitable for General Purpose Use
- Low Viscosity for Tight Fits
- Strong Shear Strength
Worn Assemblies
- Loctite 638: Useful for restoring the fit of worn assemblies. Its high strength and competent gap-filling properties offer a durable solution.
- Loctite 680: While primarily for larger gaps, it can also bond worn assemblies effectively due to its high-viscosity and strong bonding capability.
Key Differences:
Feature | Loctite 638 | Loctite 680 |
---|---|---|
Gap Fill | Up to 0.010 in (0.25 mm) | Up to 0.015 in (0.38 mm) |
Temperature Tolerance | High | Moderate |
Cure Time | Fast | Room Temperature |
Shear Strength | High (up to 4,000 psi) | High (up to 4,000 psi) |
Viscosity | Medium | High |
Application | Precision Parts | General Purpose |
When selecting between Loctite 638 and 680, consider the specific application requirements, gap size, load stress, and environmental conditions. Each product offers unique benefits that ensure optimal performance and durability in your mechanical assemblies.
User Experience And Feedback
The user experience with Loctite 638 and 680 has varied based on specific application needs. While both adhesives are renowned for their efficiency, their performance differs notably.
Success Stories
- Machinery Maintenance:
- Loctite 680: Numerous professionals have successfully used Loctite 680 for machinery maintenance due to its high strength and low viscosity. One user reported fixing a badly worn bearing with 680, restoring the machine’s functionality for years.
- Loctite 638: Users have shared success in high-load applications where Loctite 638’s thick viscosity and quick curing provided robust bonds. For instance, engineers have noted improved performance in industrial gears held together using 638.
- Automotive Repairs:
- Loctite 680: Auto mechanics often prefer Loctite 680 for its ability to bond tightly fitted parts quickly without primer. One auto shop used Loctite 680 to secure engine components, significantly reducing downtime.
- Loctite 638: Loctite 638 has also proven reliable in automotive repair. Users appreciate its strong bonding capabilities on press-fit joints, helping to maintain longevity in vehicle assemblies.
Common Issues And Solutions
- Viscosity Concerns:
- Loctite 638: Some users find 638 too thick for certain applications like gluing press-fit shafts or gears. This can lead to poor bonding. A recommended solution is to ensure precise application to avoid excess adhesive.
- Loctite 680: While Loctite 680’s low viscosity generally enhances application, it may flow too freely in some cases. Users suggest applying in a controlled environment to manage flow effectively.
- Bonding Strength:
- Loctite 638: Users have faced issues with Loctite 638 not holding well under high vibration or temperature variations. Ensuring pre-cleaned surfaces and curing at optimal temperatures can mitigate this.
- Loctite 680: Though usually robust, Loctite 680 might underperform if applied to heavily oiled or contaminated surfaces. Using a primer or thoroughly cleaning substrates before application can enhance bonding.
- Temperature Variations:
- Loctite 638: High temperatures can affect adhesion. Users recommend verifying the operational temperature range to match the adhesive’s specifications.
- Loctite 680: Loctite 680 tends to perform well in temperature variations but ensuring even application and curing time helps maintain strength.
Property | Loctite 638 | Loctite 680 |
---|---|---|
Viscosity | High, 2,500-5,000 mPa.s | Low, 200-300 mPa.s |
Cure Type | Anaerobic | Anaerobic |
Gap Fill Capacity | Up to 0.010 inches | Up to 0.015 inches |
Temperature Range | -65°F to 300°F | -65°F to 300°F |
Shear Strength (psi) | 3,000-4,000 | 4,000 |
Best for | High-load bearings, gears | Bearings, bushings, cylindrical parts |
Incorporate these insights to optimize their respective applications and ensure enduring and efficient performance.
Conclusion
Choosing between Loctite 638 and 680 hinges on your specific application needs. Loctite 638 excels in precision applications with narrow gaps and high-load environments, offering quick fixture times and oil tolerance. On the other hand, Loctite 680 is versatile for medium gaps and general-purpose use, providing excellent corrosion resistance and strong bonding even in larger gaps.
Evaluate factors like gap size, load stress, and environmental conditions to make an well-informed choice. Whether you’re dealing with machinery maintenance or automotive repairs, selecting the right adhesive ensures optimal performance and longevity for your mechanical assemblies.
Frequently Asked Questions
What are the main differences between Loctite 638 and Loctite 680?
Loctite 638 is ideal for precision applications with narrow bond gaps up to 0.010 inches, offering quick fixture times of 5 minutes. In contrast, Loctite 680 accommodates larger gaps up to 0.015 inches and cures at room temperature, making it more versatile for various conditions and applications.
Which Loctite adhesive should I choose for high-load environments?
Loctite 638 is highly suitable for high-load environments due to its high strength, thick viscosity, and excellent oil tolerance, ensuring reliable performance even in contaminated areas.
Can Loctite 680 bond tighter fits effectively?
Yes, Loctite 680 features low viscosity, making it suitable for tight fits and ensuring strong bonding even in applications requiring high shear strength and flexibility in various environmental conditions.
How does Loctite 638 prevent corrosion?
Loctite 638 provides excellent corrosion resistance by creating a durable barrier on both active and passive metals, reducing the likelihood of rust and corrosion over time, ensuring long-lasting, robust connections.
What are the common applications for Loctite 680?
Loctite 680 is commonly used for general-purpose applications, including securing cylindrical parts with medium gaps, high-strength bonding for mechanical assemblies, and maintenance tasks in machinery and automotive repairs.
How long does Loctite 638 take to cure?
Loctite 638 offers a quick fixture time of 5 minutes, providing high temperature performance and good oil tolerance, making it ideal for fast-paced, precision assembly tasks.
Is Loctite 680 suitable for use in contaminated environments?
Yes, Loctite 680 performs well even in slightly contaminated environments due to its primerless, anaerobic cure feature, ensuring reliable bonding in various industrial and mechanical applications.
Can Loctite 638 be used to bond worn assemblies?
Yes, Loctite 638 is effective in bonding worn assemblies, offering gap-filling properties and high strength to rejuvenate and secure older or slightly misshapen components.
What factors should I consider when choosing between Loctite 638 and 680?
Consider gap size, load stress, temperature resistance, oil contamination, and specific application scenarios to determine the most suitable adhesive for your mechanical assembly needs.