1 Part vs 2 Part Epoxy: Which is Right for Your Project?
When it comes to adhesives, epoxy stands out for its versatility and strength. Whether you’re tackling a DIY project or a professional repair, choosing between 1 part and 2 part epoxy can make a big difference in your results. Each type has its own unique properties and applications, so understanding the differences is crucial.
1 part epoxy offers convenience and ease of use, making it ideal for quick fixes and simple bonding tasks. On the other hand, 2 part epoxy provides superior bonding strength and durability, which is essential for more demanding applications. By knowing the strengths and weaknesses of each, you can make an well-informed choice that ensures the success of your project.
Key Takeaways
- 1 Part Epoxy vs. 2 Part Epoxy: 1 part epoxy is easy to use and requires no mixing but needs heat to cure, making it ideal for simple repairs and quick fixes. 2 part epoxy requires mixing but offers superior strength and durability, suitable for demanding applications like construction and automotive repairs.
- Epoxy Properties: Epoxy is known for its strong bonding, durability, and versatility. It resists wear and tear, chemicals, and water, making it suitable for various applications from household repairs to industrial uses.
- Advantages of 1 Part Epoxy: This type is user-friendly, reduces mixing errors, has a longer shelf life, and is ideal for minor repairs and electronics where quick, easy applications are needed.
- Advantages of 2 Part Epoxy: It provides high strength, excellent thermal and chemical resistance, and versatility in bonding diverse materials. This makes it ideal for heavy-duty applications and environments with extreme conditions.
- Choosing the Right Epoxy: Consider the project’s specific requirements, environmental factors like temperature and humidity, and budget constraints when selecting between 1 part and 2 part epoxy. Each type offers unique benefits tailored to different needs and applications.
What Is Epoxy?
Epoxy is a versatile type of adhesive or coating known for its strong bonding properties and durability. It’s made by combining an epoxy resin with a hardener or curing agent, facilitating a chemical reaction that solidifies the material. Epoxy can serve various applications, from household repairs to industrial uses.
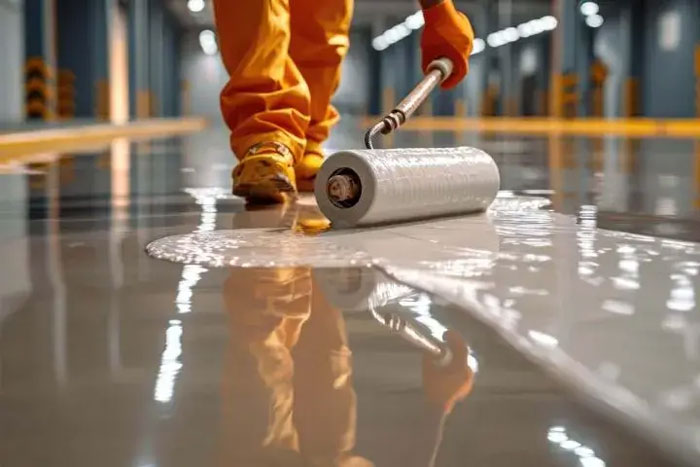
Key Terms
- Epoxy Resin: A polymer material that reacts with a hardener to produce a hardened adhesive or coating.
- Hardener: A chemical component mixed with the epoxy resin to start the curing process.
- Curing: The process where the epoxy hardens and sets, triggered by either a chemical reaction or heat.
- One-Part Epoxy: A type of epoxy that requires no mixing and cures when exposed to heat.
- Two-Part Epoxy: A type of epoxy requiring the mixing of resin and hardener to initiate the curing process.
Applications of Epoxy
- Surface Coating: Used on floors and countertops for a durable and glossy finish.
- Adhesives: Utilized in construction, automotive, and aerospace industries for strong bonding.
- Sealants: Effective for sealing cracks and joints to prevent leaks and damage.
- Electrical Systems: Acts as an insulator and protects electronic components.
Properties and Advantages
- Durability: Epoxy resists wear and tear, chemicals, and water.
- Strength: Provides a robust bond and strong adhesion to various surfaces.
- Versatility: Suitable for numerous applications across different industries.
- Heat Resistance: Maintains its properties under high temperatures.
Use Case | One-Part Epoxy | Two-Part Epoxy |
---|---|---|
Home Repairs | Simple fixes requiring minimal tools | Longer-lasting solutions requiring precision |
Automotive | Fast repairs under heat | Structural repairs needing maximum strength |
Industrial | Quick applications in manufacturing | Custom, durable bonding in critical assemblies |
The type of epoxy you select depends on your specific needs. One-part epoxy is straightforward but requires heat to cure, making it ideal for quick applications in heated environments. Conversely, two-part epoxy, which cures at room temperature, offers stronger and more enduring bonds, suitable for demanding tasks.
Key Differences Between 1 Part and 2 Part Epoxy
When choosing between 1 part and 2 part epoxy, understanding the key differences can help you make an well-informed choice. Each type has unique characteristics suitable for different applications.
Composition and Mixing
- 1 Part Epoxy: Comes pre-mixed and requires no additional mixing. Contains an initiator activated by heat, triggering the curing process.
- Example: Use straight from the tube, no need for metering or degassing.
- 2 Part Epoxy: Consists of two separate components: a resin and a hardener. Mixing these components is necessary to start the curing process. The correct mixing ratio is crucial.
- Example: Requires mechanical or manual mixing of resin and hardener, initiates an exothermic reaction forming a strong bond.
Curing Process
- 1 Part Epoxy: Requires heat to cure. Usually cured in an oven or with another heating mechanism.
- Temperature: Typical curing temperatures range from 125°C to 150°C.
- Time: Curing time can vary from minutes to hours depending on the specific epoxy type and temperature.
- 2 Part Epoxy: Cures at room temperature, although additional heat can expedite the process.
- Room Temperature Curing: About 24-48 hours.
- Accelerated Curing: Heat can reduce curing time to a few hours.
Application and Usage
- 1 Part Epoxy: Ideal for applications requiring simplicity and ease of use.
- Examples: Electronics, simple bonding jobs, and minor repairs.
- 2 Part Epoxy: Suited for more demanding tasks that need a stronger bond.
- Examples: Construction, automotive repairs, and industrial applications.
Property | 1 Part Epoxy | 2 Part Epoxy |
---|---|---|
Composition | Pre-mixed | Requires mixing resin and hardener |
Activation | Heat | Mixing initiates curing |
Curing Temperature | Typically 125°C to 150°C | Room temperature, can use heat to speed up |
Curing Time | Variable, usually minutes to hours | 24-48 hours at room temperature, faster with heat |
Usability | Simple, requires no mixing | Requires precise mixing, more preparation |
Strength | Moderate strength for simple tasks | High strength for demanding applications |
In choosing the right epoxy, consider the specific requirements of your project. The simplicity of 1 part epoxy suits quick fixes, while the strength of 2 part epoxy meets more robust needs.
Advantages of 1 Part Epoxy
When comparing adhesives, 1 part epoxy stands out for its simplicity and effectiveness. Its pre-mixed formulation streamlines the application process. Below, we’ll explore the key advantages of using 1 part epoxy.
Ease of Use
1 part epoxy excels in user convenience.
- No Mixing Required: One-component epoxies eliminate the need for mixing with a hardener. This simplifies the application process by removing the need for measuring and blending.
- Straight from the Tube: These epoxies come ready to use directly from the container. If you’re inexperienced with mixing chemicals, this aspect makes it more accessible and less intimidating.
Reduced Human Error
Using 1 part epoxy reduces the chance for mistakes.
- Elimination of Mixing Errors: Since there’s no need for mixing, the risk of incorrect resin and hardener ratios disappears. This minimizes errors that could lead to weak bonds or improper curing.
- Consistent Application: Without the need for mixing, the application process becomes more consistent. This leads to reliable and predictable results every time.
Storage and Shelf Life
1 part epoxy offers practical benefits in terms of storage.
- Longer Shelf Life: These adhesives generally have a longer shelf life compared to 2 part epoxies. There’s no risk of the components reacting prematurely since the mixture is pre-stabilized.
- Simpler Storage Requirements: You only need to store one container, making it easier to manage and organize.
Summarizing, 1 part epoxy is user-friendly, reduces the risk of errors, and features convenient storage options. Whether you’re tackling minor repairs or involved in detailed electronics work, 1 part epoxy provides a hassle-free solution.
Advantages of 2 Part Epoxy
Superior Strength
2-part epoxies offer unparalleled strength compared to 1-part variants. This superiority stems from their unique curing process. When resin combines with a hardener, an exothermic reaction occurs, forming strong molecular bonds through cross-linking. This reaction generates a tough, molded plastic-like substance.
Key Benefits:
- Cross-Linking: Forms robust molecular bonds
- Durability: Endures high stress and load
- Adhesion: Bonds diverse materials effectively
For example, in applications requiring high-strength bonds like construction or automotive repairs, 2-part epoxies provide reliable performance.
Versatility in Applications
2-part epoxies are versatile, allowing for bonding a wide array of materials. Mixing resin and hardener initiates a chemical reaction that bonds to almost any surface. This flexibility makes them suitable for various projects.
Common Uses:
- Flooring: Durable coatings for high-traffic areas
- Tabletops: Creates glossy, resistant surfaces
- Deep Pours: Ideal for resin art and large molds
Unlike 1-part epoxies, which are limited to specific uses, 2-part versions adapt to multiple scenarios, including bonding metals, plastics, ceramics, and wood.
Thermal and Chemical Resistance
2-part epoxies stand out because of their thermal and chemical resistance. Once cured, they withstand extreme temperatures and harsh chemicals without losing integrity.
Performance Metrics:
- Thermal Resistance: Operates effectively between -40°F and 300°F (-40°C and 149°C)
- Chemical Resistance: Withstands acids, bases, and solvents
These properties make 2-part epoxies ideal for environments exposed to fluctuating temperatures and chemicals, including industrial settings and marine applications.
Comparison Table
Here’s a quick comparison of key properties between 1-part and 2-part epoxies:
Property | 1-Part Epoxy | 2-Part Epoxy |
---|---|---|
Strength | Moderate | High |
Ease of Use | Mix-free | Requires mixing |
Curing Temperature | Requires heat (~150°C) | Room temperature |
Versatility | Limited | Extensive |
Thermal Resistance (°F) | Up to 150°F | -40°F to 300°F |
Chemical Resistance | Moderate | High |
Shelf Life | Longer | Shorter once mixed |
Common Applications | Electronics, Repairs | Construction, Automotive |
Summary
2-part epoxies excel in strength, versatility, and resistance, making them invaluable for demanding tasks. Always consider the specific requirements of your project when choosing between 1-part and 2-part epoxies.
Choosing the Right Epoxy for Your Project
Selecting the appropriate epoxy requires understanding project requirements, environmental factors, and budget considerations. Each aspect ensures the epoxy performs optimally for your specific needs.
Project Requirements
Application and Use:
- 1-Part Epoxy: Ready to use from the container, 1-part epoxies cure with heat, which can streamline processes requiring thermal cycles. Ideal for assembly lines and minor repairs, these epoxies simplify application due to no mixing required.
- 2-Part Epoxy: These epoxies necessitate mixing resin and hardener, initiating a chemical reaction that cures the adhesive. Suitable for a broad range of applications, from construction to artistic endeavors, they offer versatility and strong bonding.
Environmental Factors
Environmental factors such as temperature, humidity, and exposure to chemicals influence epoxy selection.
- Temperature:
- 1-Part Epoxy: Often requires elevated temperatures for curing, making them unsuitable for projects done in ambient conditions without access to curing ovens.
- 2-Part Epoxy: Offers flexibility with curing at room temperature or accelerated with heat, accommodating diverse environmental conditions.
- Humidity:
- 1-Part Epoxy: Sensitive to moisture during the curing process, which can affect bond strength; appropriate for controlled environments.
- 2-Part Epoxy: Generally more tolerant of humidity variations, providing reliable performance across different settings.
- Chemical Exposure:
- 1-Part Epoxy: Less resistant to harsh chemicals, suitable for environments with minimal chemical exposure.
- 2-Part Epoxy: Exhibits excellent resistance to chemicals; optimal for industrial applications where exposure is significant.
Budget Considerations
Balancing cost with performance ensures you choose an epoxy that meets both financial and functional needs.
- 1-Part Epoxy:
- Typically more affordable due to simpler formulation and storage.
- Reduced labor costs because of the elimination of mixing steps.
- Long shelf life, reducing wastage and frequency of purchase.
- 2-Part Epoxy:
- Higher initial cost due to the complexity of resin and hardener formulation.
- Potentially higher labor costs from mixing requirements.
- Superior performance justifies investment for demanding applications.
Property | 1-Part Epoxy | 2-Part Epoxy |
---|---|---|
Ease of Use | Ready to use, no mixing required | Requires mixing resin and hardener |
Curing Temperature | Elevated temperature needed for curing | Room temperature or heat-accelerated curing |
Bond Strength | Moderate, adequate for minor repairs | High, suitable for structural applications |
Chemical Resistance | Limited | Excellent resistance against various chemicals |
Shelf Life | Long, simple storage | Dependent on proper mixing and storage conditions |
Cost | Lower initial cost, reduced labor costs | Higher initial and potential labor costs |
Versatility | Specific applications with less flexibility | Broad applications, from construction to art |
This detailed breakdown guides you in choosing between 1-part and 2-part epoxies. By considering project specifics, environmental impacts, and budget limits, you can make an well-informed choice tailored to your requirements.
Conclusion
Choosing between 1 part and 2 part epoxy eventually comes down to your project’s specific needs. If you’re looking for convenience and ease of use for minor repairs or electronics, 1 part epoxy is a great choice. It’s ready to use without the hassle of mixing and offers a longer shelf life.
On the other hand, for projects requiring superior strength and durability, 2 part epoxy is unmatched. Its ability to bond various materials and withstand extreme conditions makes it ideal for construction, automotive repairs, and industrial applications.
By understanding the unique properties and applications of both types of epoxy, you can make an well-informed choice that ensures the success of your project.
Frequently Asked Questions
What is the main difference between 1 part and 2 part epoxy?
1 part epoxy is pre-mixed and cures with heat, making it convenient for quick fixes. In contrast, 2 part epoxy requires mixing resin and hardener in precise ratios, offering stronger bonds ideal for more demanding tasks.
Can 1 part epoxy be used for industrial applications?
1 part epoxy is typically not recommended for industrial applications due to its lower bonding strength and durability compared to 2 part epoxy. It’s better suited for minor repairs and electronics.
How does the curing process differ between 1 part and 2 part epoxy?
1 part epoxy requires heat to cure, often in an oven at higher temperatures. On the other hand, 2 part epoxy cures at room temperature but can also be accelerated with heat.
Which type of epoxy is more user-friendly?
1 part epoxy is more user-friendly as it comes pre-mixed, eliminating the need for precise measurements and mixing, thus reducing the chance of human error.
What are the advantages of 2 part epoxy over 1 part epoxy?
2 part epoxy offers superior strength, versatility, and excellent thermal and chemical resistance, making it suitable for demanding applications like construction and automotive repairs.
Is 1 part epoxy more affordable than 2 part epoxy?
Generally, 1 part epoxy is more affordable. However, 2 part epoxy may justify its higher cost through superior performance in demanding applications.
Can you apply a new layer of epoxy over an old one?
Yes, you can apply a new layer of epoxy over an old one, but the existing surface must meet certain criteria for adhesion. Proper surface preparation is crucial for successful application.
What should be considered when choosing the right epoxy for a project?
Consider project requirements, environmental factors (temperature, humidity, chemical exposure), and budget. 1 part epoxy is ideal for controlled environments, while 2 part offers versatility and strong bonding across various applications.
Does 2 part epoxy have a long shelf life?
Yes, 2 part epoxy can have a long shelf life if the resin and hardener are properly stored at room temperature in closed containers to prevent contamination.